Selecting the correct air compressor size for air tools is crucial for operational efficiency and longevity of both the compressor and tools. This guide will help you understand the factors affecting air compressor size and how to select the right one for your needs.
Determining Your Air Compressor Needs
Assessing CFM Requirements
The primary factor in choosing an air compressor is its Cubic Feet Per Minute (CFM) output, which should align with the CFM requirements of your air tools. Tools like sanders, grinders, and pneumatic saws have specific CFM needs that must be met for optimal performance.
To accurately determine your CFM requirements:
- Identify the CFM rating for your most demanding air tool. This information can usually be found in the tool’s user manual or specifications.
- Check if the CFM rating is for 100% duty cycle. Many continuous-use tools are rated assuming only 50-60% usage. If you plan to use the tool continuously, you’ll need a higher CFM rating.
- If you intend to use multiple tools simultaneously, add up the individual CFM requirements to calculate your total CFM need.
Once you know the CFM requirements of your most demanding tool or combination of tools, you can select an air compressor with a CFM output that meets or slightly exceeds that number.
For more detailed insights on air tool CFM requirements, VMAC’s air tool CFM chart provides a comprehensive guide.
100% Duty Cycle Compressors
For continuous use tools, a 100% duty cycle compressor is essential. This type of compressor can run indefinitely without needing a break, ensuring uninterrupted work flow. Air compressors with a 30-40 CFM, 60-70 CFM, or 90-100 CFM at 100% duty cycle are ideal for various industrial applications.
When selecting a 100% duty cycle compressor, consider the following:
- Rotary screw compressors are typically better suited for 100% duty cycle operation compared to reciprocating compressors.
- Oil-injected rotary screw compressors offer better cooling and lubrication for continuous use.
- Variable speed drive (VSD) compressors can adjust output to match demand, saving energy during periods of lower air consumption.
Choosing the Right Size
Small to Medium CFM Compressors
For light to medium-duty tasks, a 30-40 CFM air compressor might suffice, especially for tasks like tire inflation or small tool operation. These compressors are typically portable and well-suited for home garages, small workshops, or mobile service trucks.
When considering a small to medium CFM compressor:
- Opt for a model with a tank size of at least 20 gallons for better air storage and less frequent cycling.
- Consider an oil-free compressor for easier maintenance if usage will be infrequent.
- Look for a compressor with a maximum PSI rating of at least 125 for versatility with different tools.
Learn about the versatility of these compressors on What Size Air Compressor Do I Need For Air Tools? – VMAC.
High Capacity Compressors
For more demanding operations, a high capacity air compressor, such as a 60-70 CFM or 90-100 CFM air compressor, is necessary. These are suited for heavy-duty industrial use and can handle larger tools like 1″ impact wrenches and 90 lb jackhammers.
When selecting a high capacity compressor:
- Choose between a stationary or portable model based on your needs. Stationary compressors offer more power, while portable units provide flexibility.
- Consider a two-stage compressor for better efficiency and higher PSI output.
- Look for features like an aftercooler, automatic tank drains, and low oil shutdown to protect and extend the life of the compressor.
For an in-depth guide on selecting high-capacity compressors, check out Landmark Tools’ air compressor guide.
Evaluating Air Compressor Duty Cycle
Understanding the duty cycle of an air compressor is crucial for selecting the right model. An luftkompressor with a 100% duty cycle, like those mentioned in SGS Engineering’s article, can operate continuously, making it ideal for extensive use.
The duty cycle represents the percentage of time a compressor can operate without overheating. For example:
- A 50% duty cycle means for every 10 minutes of use, the compressor must rest for 10 minutes.
- A 75% duty cycle allows 45 minutes of runtime per hour, with 15 minutes of rest.
- A 100% duty cycle enables nonstop operation without required downtime.
To determine the right duty cycle for your needs:
- Estimate the longest continuous runtime you’ll need from your air compressor.
- Allow for a margin of error by selecting a compressor with a duty cycle slightly higher than your maximum estimated runtime.
- Consider a compressor with a 100% duty cycle for demanding applications or if future needs may increase.
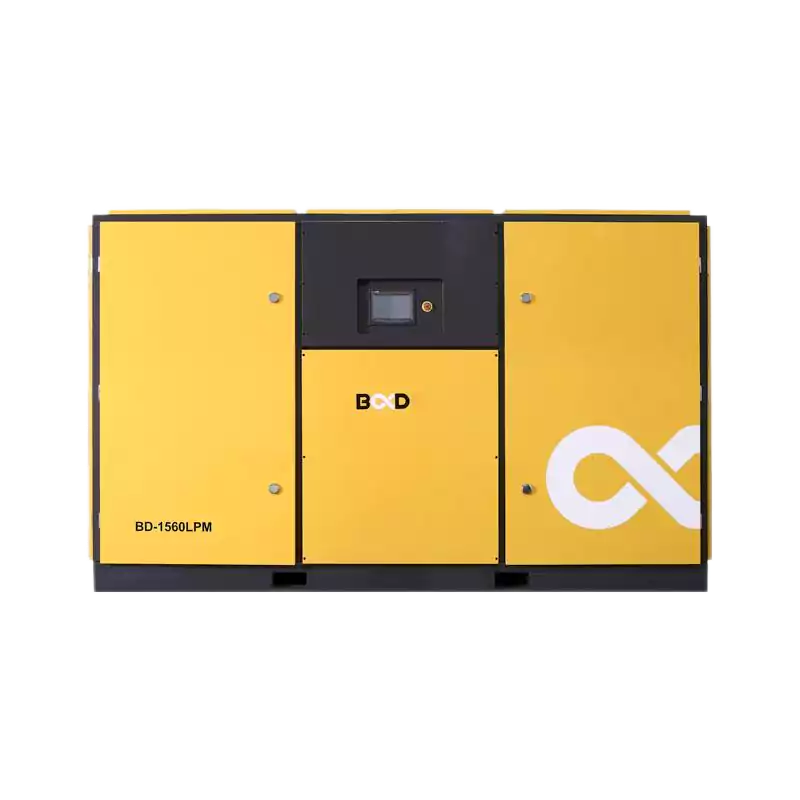
Ofte stillede spørgsmål
Q: What does CFM stand for?
EN: CFM stands for Cubic Feet per Minute, indicating the volume of air an air compressor delivers per minute.
Q: Why is duty cycle important in choosing an air compressor?
EN: The duty cycle determines how long an air compressor can operate continuously. A 100% duty cycle compressor can run indefinitely without needing to rest, which is vital for heavy-duty operations.
Q: Can I use a single air compressor for multiple tools?
EN: Yes, but ensure the compressor’s CFM output meets the combined CFM requirements of all tools used simultaneously. For guidance, BigRentz’s air compressor size article offers valuable information.
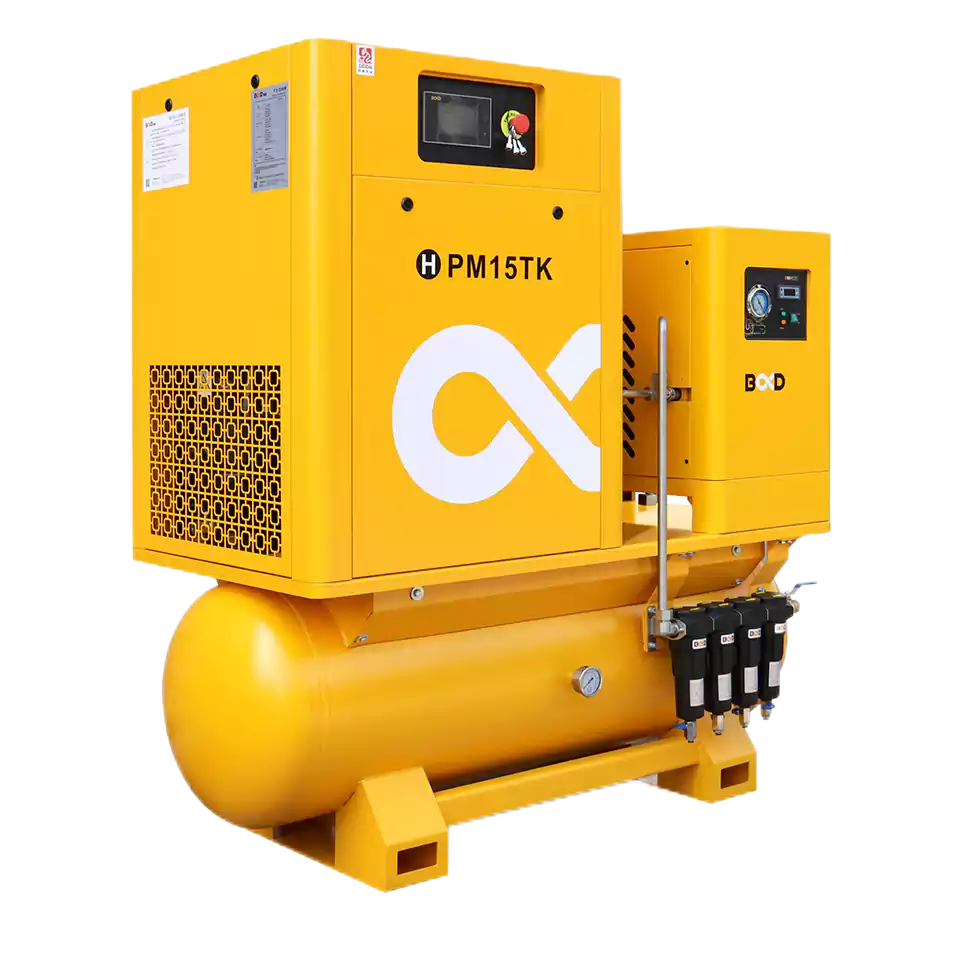
In conclusion, selecting the right air compressor involves understanding your tools’ CFM requirements, considering the duty cycle, and evaluating the size and type of compressor needed. With the right knowledge, you can ensure efficient and effective use of your air tools.
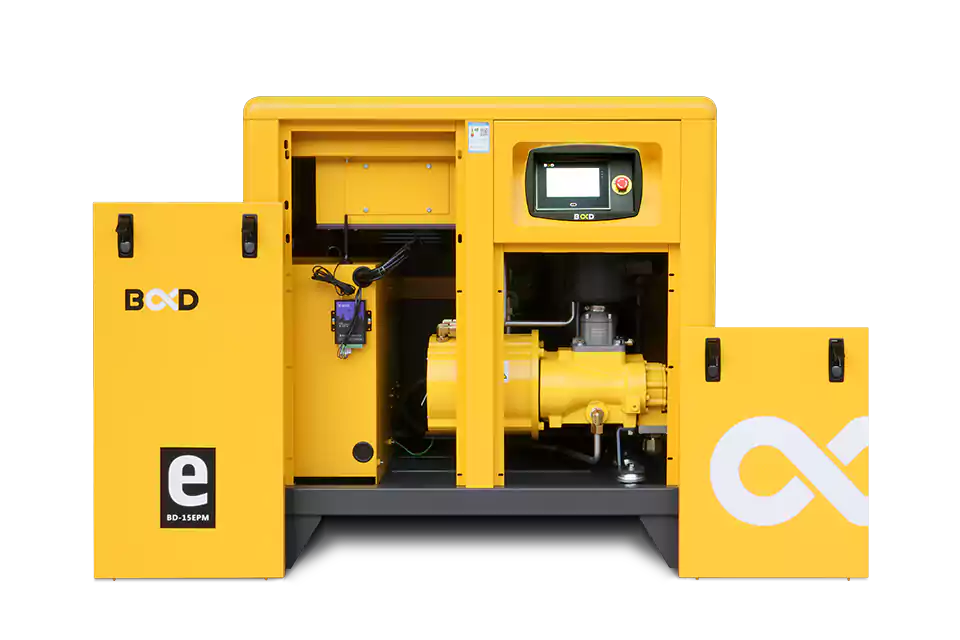
Meta Description: Learn how to select the ideal air compressor size for your air tools with our comprehensive guide, covering CFM requirements, duty cycle, and tips for choosing between different compressor capacities.