Introduction
Rotary screw air compressors are essential for various industrial applications due to their efficiency and reliability. However, like all mechanical devices, they can encounter issues. Understanding common problems and maintenance techniques can significantly enhance their performance and longevity.
Rotary screw compressors are widely used in manufacturing, automotive, and other heavy industries because of their ability to provide a continuous supply of compressed air. They are known for their durability, low noise levels, and energy efficiency compared to other types of air compressors, such as scroll air compressors.
Despite their many advantages, rotary screw compressors can experience problems if not properly maintained. Regular inspections, timely repairs, and following manufacturer guidelines are crucial for optimal performance and preventing costly downtime.
In this article, we will explore the most common issues faced by rotary screw air compressors and provide practical solutions to address them. We will also discuss preventive maintenance tips to keep your compressor running smoothly and efficiently.
Common Problems and Solutions
Compressor Oil Issues
One frequent issue is compressor oil leaking. This can affect the compressor’s efficiency and damage other parts if not addressed promptly. Oil leaks can occur due to worn-out seals, damaged gaskets, or improper installation of components.
Regular checks for oil leaks and maintaining proper oil levels are crucial. Inspect the compressor for any visible signs of leakage, such as oil puddles or stains. If you detect a leak, identify the source and replace the faulty seals or gaskets. Ensure that you use the correct type and grade of oil recommended by the manufacturer.
Another oil-related problem is oil contamination. Contaminants like dust, moisture, or debris can mix with the oil and cause damage to the compressor’s internal parts. To prevent this, regularly change the oil and oil filters according to the manufacturer’s guidelines. Use high-quality, clean oil and store it properly to avoid contamination.
For in-depth troubleshooting on oil-related issues, see “10 Air Compressor Problems & Solutions”.
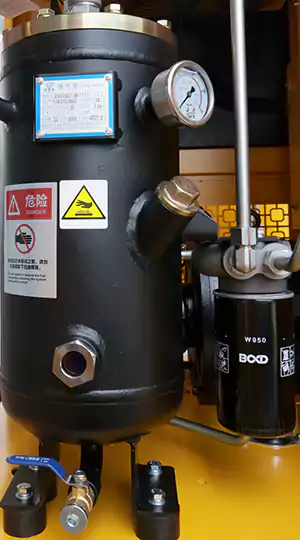
Temperature Regulation Problems
High ambient temperature can lead to overheating, which is a common problem in rotary screw compressors. Overheating can cause the compressor to shut down, leading to production downtime and potential damage to internal components.
To prevent overheating, ensure sufficient ventilation around the compressor and check if the cooling systems, such as fans and air ducts, are functioning correctly. Clean the coolers and radiators regularly to remove any dirt or debris that may hinder heat dissipation.
Monitor the compressor’s temperature gauges and set the temperature controls according to the manufacturer’s recommendations. If the compressor frequently overheats despite proper ventilation and cooling, there might be an underlying issue with the temperature sensors or thermostatic valves, which require professional inspection and repair.
For more on managing temperatures in compressors, refer to “Rotary screw air compressor troubleshooting basics”.
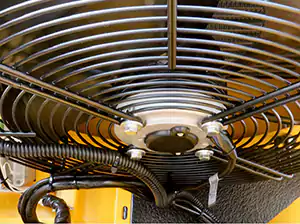
Electrical and Control Issues
Electrical power issues and control circuit problems can prevent compressors from operating efficiently. Electrical faults can cause the compressor to trip or not start at all. Control issues can lead to erratic behavior, such as the compressor not loading or unloading properly.
Regular electrical system inspections are necessary to identify any loose connections, damaged wires, or faulty components. Check the power supply voltage and ensure it matches the compressor’s requirements. Inspect the starter, contactors, relays, and overload protection devices for any signs of wear or malfunction.
For control issues, check the pressure switch settings and adjust them if necessary. Ensure that the solenoid valves and inlet valves are functioning correctly. Inspect the control panel for any error codes or warning lights that may indicate a specific problem.
Learn more about electrical troubleshooting in “Rotary Screw Compressor Troubleshooting”.
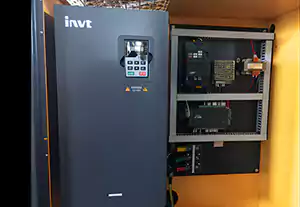
Mechanical and Structural Concerns
Uneven mounting bolts and compressor vibration issues can also lead to operational disruptions. Loose or uneven mounting can cause excessive vibration, leading to premature wear of components and potential leaks.
Regularly check the mounting bolts and ensure they are tightened to the manufacturer’s torque specifications. Use a vibration meter to measure the compressor’s vibration levels and compare them to the acceptable limits. If the vibration is excessive, inspect the motor bearings, couplings, and other rotating parts for any damage or misalignment.
Structural issues like cracks in the compressor housing or damaged piping can also affect performance and lead to leaks. Conduct visual inspections of the compressor’s external parts and look for any signs of damage, corrosion, or wear. Address any structural problems promptly to prevent further deterioration.
Detailed guidance can be found in “4 Air Compressor Problems: A Complete Troubleshooting”.
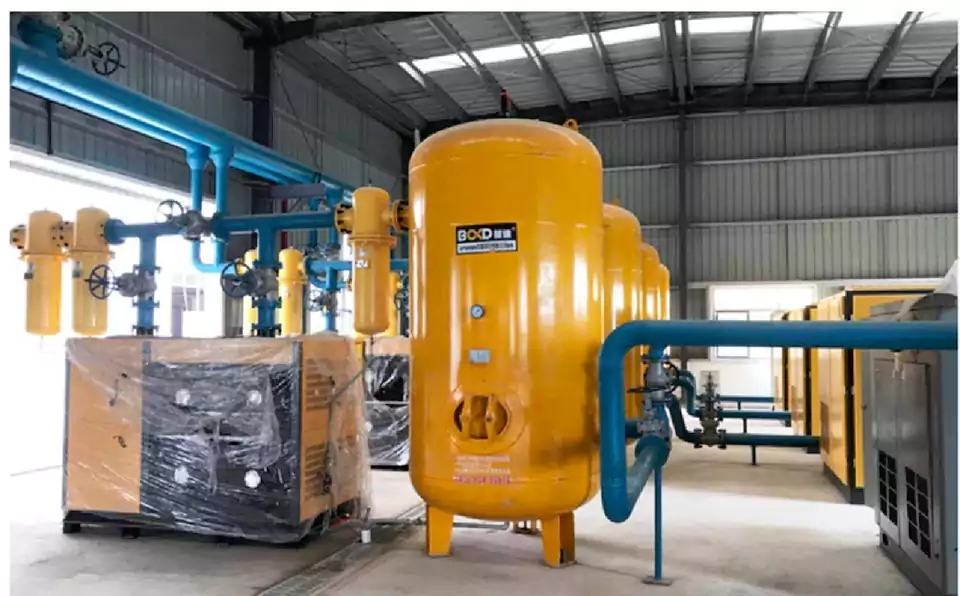
Preventative Maintenance Tips
Regular Inspections
Regularly inspect and replace worn parts such as filters and separators. Air filters prevent contaminants from entering the compressor, while oil filters and separators ensure clean oil circulation. Replace these components according to the manufacturer’s recommended intervals or sooner if they appear dirty or clogged.
Keep an eye on the oil cooler and clean it as needed to prevent clogs, as suggested in the “Air Compressor Troubleshooting Guide”. A dirty oil cooler can lead to overheating and reduced efficiency.
Inspect the compressor’s piping, hoses, and fittings for any signs of wear, cracks, or leaks. Replace any damaged parts to prevent air leaks and ensure optimal performance.
Lubrication
Lubrication is essential for the smooth operation of rotary screw compressors. The lubricant reduces friction, prevents wear, and helps dissipate heat. Use the correct type of oil recommended by the manufacturer, as using the wrong oil can lead to damage and void the warranty.
Change the oil and oil filters at the intervals specified in the maintenance manual. Regularly check the oil level and top it up if necessary. Monitor the oil’s condition and look for any signs of contamination, such as discoloration or presence of debris. If the oil appears dirty or degraded, replace it promptly.
Proper lubrication not only extends the life of the compressor but also improves its efficiency and performance. Consider using high-quality lubricants specifically designed for rotary screw air compressors to ensure optimal performance.
Operational Checks
Perform routine operational checks to ensure settings like pressure and temperature are within normal ranges. Monitor the compressor’s gauges and control panel for any abnormal readings or warning indicators.
Check the compressor’s load and unload cycles to ensure they are functioning correctly. The compressor should load when the system pressure drops below the set point and unload when the pressure reaches the upper limit. Abnormal loading or unloading behavior can indicate issues with the pressure switch, solenoid valves, or control system.
Regularly drain condensate from the air receiver tank and moisture separators to prevent corrosion and maintain air quality. Ensure that the drain valves are functioning properly and not clogged.
For common operational issues and their solutions, explore “Common faults and solution for screw air compressor”.
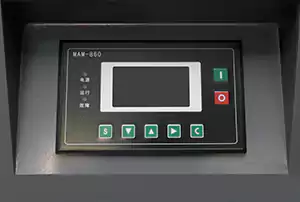
Frequently Asked Questions
Q1: How often should I check the oil level in my rotary screw compressor?
A1:Check the oil level at least once a week and top up if necessary. Regularly monitoring the oil level helps prevent low oil conditions that can damage the compressor.
Q2: What should I do if my compressor starts making unusual noises?
A2:Investigate the cause of the noise immediately as it could indicate loose parts, worn bearings, or other mechanical issues. Refer to the troubleshooting guide in your compressor’s manual for specific steps to identify and resolve the problem. If the noise persists or you are unsure about the cause, contact a professional service technician.
Q3: How can I prevent my air compressor from overheating?
A3:Ensure good ventilation around the compressor, perform regular maintenance of cooling components, and check ambient temperature conditions. Keep the coolers and radiators clean and free from dirt or debris. Monitor the compressor’s temperature gauges and address any overheating issues promptly to prevent damage to internal parts.
Oil Leakage Prevention and Control
Oil leakage is a common problem in rotary screw air compressors that can lead to reduced efficiency, increased maintenance costs, and potential damage to the compressor and downstream equipment. Preventing and controlling oil leaks is crucial for the optimal performance and longevity of your compressor.
Here are some key methods for preventing and addressing oil leaks in your rotary screw air compressor:
- Proper Installation of Gaskets: Ensure that gaskets between compressor parts are installed correctly, using materials that meet the required specifications. Improper gasket installation or using low-quality materials can lead to leaks under pressure.
- Correct Tightening of Fittings: Tighten nuts and bolts to the manufacturer’s recommended torque values. Over-tightening can cause metal deformation around the screw holes, while under-tightening may allow leaks to occur under pressure.
- Timely Replacement of Oil Seals: Replace worn or damaged oil seals promptly. Aging seals can lose their elasticity and cause misalignment, leading to oil leaks.
- Regular Replacement of Wear Parts: Replace worn components such as piston rings and cylinder liners as needed. Wear in these parts can allow high-pressure air to escape into the crankcase, forcing oil out of the compressor.
- Maintaining Check Valves and Vent Valves: Ensure that check valves and vent valves are not blocked. Blockages can cause pressure buildup in the oil reservoir, leading to leaks through weak seals.
- Proper Sealing of Oil Lines: Regularly inspect and tighten oil line connections. Loose fittings or damaged flare seals can cause oil leaks. If necessary, replace damaged oil lines to ensure proper sealing.
- Avoiding Overfilling: Fill the compressor with the correct amount of oil as specified by the manufacturer. Overfilling can cause oil to be carried out with the compressed air, leading to excessive oil consumption and leaks.
By implementing these preventive measures and promptly addressing any oil leaks that occur, you can minimize the impact of oil leakage on your rotary screw air compressor’s performance and maintain a clean, efficient compressed air system.
For more information on causes and solutions for oil leakage, refer to “Causes And Solutions For Oil Leakage Of Air Compressor Oil”.
Conclusion
Rotary screw air compressors are reliable workhorses in various industrial applications, but they require regular maintenance and prompt troubleshooting to ensure optimal performance and longevity. By understanding common problems like oil leaks, temperature issues, electrical faults, and mechanical concerns, you can take proactive steps to prevent and address them.
Implementing a comprehensive preventive maintenance program that includes regular inspections, lubrication, and operational checks is essential for keeping your rotary screw compressor running smoothly and efficiently. Following the manufacturer’s guidelines and using genuine rotary screw compressor parts can help prevent premature wear and failures.
If you encounter persistent issues or are unsure about how to troubleshoot a problem, don’t hesitate to consult the compressor’s manual or seek assistance from a qualified service technician. Prompt action and proper maintenance can save you from costly downtime and extend the life of your rotary screw air compressor.
By staying informed about common issues, implementing preventive measures, and addressing problems promptly, you can ensure that your rotary screw air compressor remains a reliable and efficient asset in your industrial operations.
Meta Description
Explore essential maintenance tips and troubleshooting steps for rotary screw air compressors. Learn how to handle oil leaks, temperature issues, electrical problems, and more to enhance your compressor’s performance and durability.