Introduction to Air Compressor Technologies
Air compressors are essential in various industrial applications, providing the power necessary for tools and processes. The choice between variable-speed and fixed-speed compressors is crucial, impacting efficiency, cost, and operational suitability.
Air compressor technology has evolved significantly over the years to meet the growing demands of industries. From small workshops to large manufacturing plants, air compressors play a vital role in powering pneumatic tools, operating machinery, and facilitating various processes.
The two primary types of air compressors are variable-speed and fixed-speed compressors. Variable-speed compressors, also known as Variable Frequency Drive (VFD) compressors, can adjust their motor speed to match the air demand. This technology allows for energy savings and reduced wear on the compressor components.
On the other hand, fixed-speed compressors operate at a constant speed, regardless of the air demand, which can lead to energy waste and increased mechanical stress. Understanding the differences between these two technologies is essential for making an informed decision when selecting an air compressor for your specific application.
Factors such as energy efficiency, operational stability, maintenance requirements, and initial investment should be carefully considered to ensure optimal performance and cost-effectiveness. In the following sections, we will delve deeper into the mechanisms, benefits, and considerations of both variable-speed and fixed-speed air compressors, providing you with the knowledge necessary to make the best choice for your industrial needs.
Variable Speed Compressors: Adapting to Demand
The Mechanism of Variable Speed Compressors
Variable speed compressors utilize a technology known as a Variable Speed Drive (VSD) to adjust the motor’s speed based on the demand for compressed air. This adaptability leads to energy savings and reduced operational costs, as the compressor consumes power proportional to the air demand, rather than operating at full capacity continuously.
The VSD technology works by continuously monitoring the air pressure in the system and adjusting the motor speed accordingly. When air demand increases, the VSD increases the motor speed to produce more compressed air. Conversely, when air demand decreases, the VSD reduces the motor speed, saving energy and minimizing wear on the compressor components.
This dynamic adjustment of motor speed is made possible by the VSD’s ability to control the frequency and voltage of the electrical power supplied to the motor. By varying the frequency, the VSD can regulate the motor’s rotational speed, allowing it to operate at optimal levels based on the air demand.
The VSD also enables soft starting and stopping of the compressor, which reduces mechanical stress on the motor and other components. This feature helps extend the lifespan of the compressor and minimizes maintenance requirements. Furthermore, variable speed compressors can maintain a more consistent air pressure within a narrow range, ensuring stable operation of pneumatic tools and processes. This precise pressure control enhances the overall efficiency and quality of the compressed air system.
Benefits of Variable Speed Technology
- Energy Efficiency: Variable speed compressors are known for their ability to significantly reduce energy consumption, especially in systems with fluctuating air demand.
- Operational Stability: By adjusting motor speed, these compressors maintain a constant air pressure, which is vital for consistent operation in industrial environments.
- Reduced Wear and Tear: The soft start and stop reduce mechanical stress, extending the lifespan of the compressor components.
Variable speed technology offers several significant benefits for industrial compressed air systems:
- Energy Efficiency: By matching the motor speed to the air demand, variable speed compressors can achieve substantial energy savings compared to fixed-speed compressors. Studies have shown that variable speed compressors can reduce energy consumption by up to 50% in applications with varying air demand. This energy efficiency translates into lower operating costs and a reduced environmental impact.
- Operational Stability: Variable speed compressors maintain a constant air pressure within a narrow range, typically ±0.1 bar. This precise pressure control ensures stable operation of pneumatic tools and processes, improving product quality and reducing scrap rates. The consistent air pressure also helps prevent pressure fluctuations that can cause equipment damage or unplanned downtime.
- Reduced Wear and Tear: The soft start and stop capabilities of variable speed compressors minimize mechanical stress on the motor and other components. By gradually ramping up and down the motor speed, the compressor avoids the sudden torque and current spikes associated with fixed-speed compressors. This gentle operation extends the lifespan of the compressor components, reducing maintenance requirements and increasing overall reliability.
- Improved Air Quality: Variable speed compressors often incorporate advanced control systems that optimize the performance of air treatment components, such as dryers and filters. By maintaining stable pressure and temperature conditions, these compressors help ensure consistent air quality, minimizing the risk of moisture, oil, and particulate contamination in the compressed air supply.
- Flexibility and Scalability: Variable speed compressors can adapt to changes in air demand over time, making them suitable for applications with varying production levels or future expansion plans. The VSD technology allows the compressor to operate efficiently across a wide range of air demand, providing flexibility and scalability for growing businesses.
While variable speed compressors typically have a higher initial investment compared to fixed-speed compressors, the long-term energy savings and operational benefits often justify the additional cost. The return on investment (ROI) for variable speed compressors can be achieved within a relatively short period, depending on the specific application and energy costs.
Fixed Speed Compressors: Consistency and Reliability
Overview of Fixed Speed Operation
Fixed speed compressors operate at a constant speed, providing a steady rate of air output. This design is simpler and often results in lower upfront costs and maintenance expenses.
Fixed speed compressors, also known as constant speed compressors, have been the traditional choice for many industrial applications. These compressors operate at a fixed motor speed, typically 3,600 rpm for 60 Hz electrical systems or 3,000 rpm for 50 Hz systems. The motor is directly coupled to the compressor element, which means that the compressor runs at a constant speed regardless of the air demand.
When the air demand is lower than the compressor’s output, fixed speed compressors use a load/unload control system to manage the excess air. When the system pressure reaches a predetermined upper limit, the compressor unloads, meaning that it stops compressing air but continues to run at full speed. The unloaded compressor consumes about 20-30% of its full-load power. When the system pressure drops to a lower limit, the compressor loads again and resumes compressing air.
This load/unload cycle can occur frequently in applications with varying air demand, leading to increased energy consumption and wear on the compressor components. To mitigate these issues, fixed speed compressors often incorporate additional components such as air receivers, which store compressed air and help stabilize the system pressure.
Despite their limitations in terms of energy efficiency and adaptability to varying air demand, fixed speed compressors offer several advantages:
- Lower Initial Cost: Fixed speed compressors are generally less expensive than variable speed compressors due to their simpler design and control system. This lower upfront cost can be attractive for businesses with limited capital budgets or those who prioritize initial cost over long-term energy savings.
- Proven Reliability: Fixed speed compressors have been in use for decades and have a proven track record of reliability. The simple design and fewer electronic components contribute to their robustness and durability in demanding industrial environments.
- Ease of Maintenance: The straightforward design of fixed speed compressors makes them easier to maintain compared to variable speed compressors. Maintenance tasks such as oil changes, filter replacements, and belt adjustments are generally simpler and can be performed by in-house maintenance staff.
- Suitability for Constant Air Demand: In applications where the air demand is relatively constant, fixed speed compressors can operate efficiently without the need for variable speed control. Examples include continuous manufacturing processes or facilities with a stable production output.
When to Choose Fixed Speed
- Consistent Demand: Ideal for operations with a stable demand where the air requirement is constant, allowing the compressor to operate efficiently at its designed capacity.
- Lower Initial Investment: Generally less expensive than variable speed models, making them attractive for businesses prioritizing initial cost over long-term savings.
When deciding between a fixed speed and variable speed compressor, it’s essential to consider your specific application requirements and conduct a thorough analysis of your compressed air system. Factors to evaluate include:
- Air Demand Profile: Assess the variability of your air demand over time. If your air demand fluctuates significantly, a variable speed compressor may offer substantial energy savings. However, if your air demand is relatively constant, a fixed speed compressor can be a cost-effective choice.
- Energy Costs: Consider the cost of electricity in your area and the potential energy savings offered by variable speed compressors. In regions with high energy costs, the long-term savings from a variable speed compressor can be significant, justifying the higher initial investment.
- Facility Size and Expansion Plans: Evaluate your current facility size and future expansion plans. Variable speed compressors offer greater flexibility and scalability, allowing you to adapt to changes in air demand as your business grows. Fixed speed compressors may be suitable for smaller facilities with stable air requirements.
- Maintenance Capabilities: Assess your in-house maintenance capabilities and the availability of skilled technicians. Fixed speed compressors generally require less specialized maintenance compared to variable speed compressors, which may be a consideration for facilities with limited technical resources.
- Environmental Goals: Consider your company’s environmental sustainability goals. Variable speed compressors can significantly reduce energy consumption and carbon emissions, aligning with corporate initiatives to minimize environmental impact.
Consulting with compressed air system experts and conducting a comprehensive air audit can help you make an informed decision based on your unique needs and priorities. By carefully evaluating your application requirements and considering the long-term implications of your choice, you can select the most suitable compressor technology for your industrial operations.
Comparing Variable and Fixed Speed Compressors
Performance and Cost Implications
The choice between a variable and fixed speed compressor should consider operational demands and cost implications. Variable speed compressors, while more expensive upfront, can offer significant energy savings and operational benefits in the right conditions.
When comparing variable speed and fixed speed compressors, it’s crucial to consider both performance and cost implications to make an informed decision for your specific application.
Performance Implications:
- Energy Efficiency: Variable speed compressors offer superior energy efficiency compared to fixed speed compressors, especially in applications with fluctuating air demand. By matching the motor speed to the air demand, variable speed compressors can reduce energy consumption by up to 50%. This energy efficiency translates into lower operating costs and a reduced environmental impact.
- Pressure Stability: Variable speed compressors maintain a more stable system pressure, typically within ±0.1 bar, ensuring consistent performance of pneumatic tools and processes. This pressure stability enhances product quality, reduces scrap rates, and minimizes the risk of equipment damage due to pressure fluctuations.
- Air Quality: The advanced control systems in variable speed compressors optimize the performance of air treatment components, such as dryers and filters, ensuring consistent air quality. This is particularly important in applications sensitive to moisture, oil, or particulate contamination.
- Noise Levels: Variable speed compressors generally operate at lower noise levels compared to fixed speed compressors due to their ability to adjust motor speed based on air demand. This can be a significant advantage in facilities with strict noise regulations or those located in residential areas.
Cost Implications:
- Initial Investment: Variable speed compressors typically have a higher initial cost compared to fixed speed compressors due to their advanced technology and control systems. The price difference can vary depending on the compressor size, brand, and features, but variable speed compressors can cost 20-30% more than their fixed speed counterparts.
- Energy Costs: The energy savings achieved by variable speed compressors can significantly offset the higher initial investment over time. In applications with varying air demand, variable speed compressors can reduce energy costs by 30-50%, resulting in a relatively short payback period. The actual energy savings will depend on factors such as the air demand profile, energy rates, and operating hours.
- Maintenance Costs: Variable speed compressors may have slightly higher maintenance costs due to their more complex control systems and electronics. However, the soft start and stop capabilities of variable speed compressors reduce mechanical stress on components, potentially extending their lifespan and reducing overall maintenance requirements.
- Total Cost of Ownership (TCO): When evaluating the cost implications of variable speed and fixed speed compressors, it’s essential to consider the total cost of ownership over the compressor’s lifetime. This includes the initial investment, energy costs, maintenance expenses, and any potential downtime costs. In many cases, the long-term energy savings and operational benefits of variable speed compressors outweigh the higher initial cost, resulting in a lower TCO.
To determine the most cost-effective option for your specific application, conduct a thorough analysis of your compressed air system, including an assessment of your air demand profile, energy rates, and maintenance requirements. Consult with compressed air system experts and request a detailed cost comparison from compressor manufacturers to make an informed decision based on your unique needs and priorities.
Environmental Impact
Variable speed compressors are often more environmentally friendly due to their energy-efficient nature, aligning with sustainability goals of many modern businesses.
In today’s world, businesses are increasingly focused on reducing their environmental impact and promoting sustainable practices. Compressed air systems, being significant energy consumers in industrial facilities, play a crucial role in achieving these sustainability goals. Variable speed compressors, with their energy-efficient operation, offer a more environmentally friendly solution compared to fixed speed compressors.
Energy Efficiency and Carbon Footprint:
The primary environmental benefit of variable speed compressors lies in their energy efficiency. By matching the motor speed to the air demand, variable speed compressors can reduce energy consumption by up to 50% compared to fixed speed compressors. This energy efficiency directly translates into a lower carbon footprint, as less energy consumption means reduced greenhouse gas emissions from power generation.
For example, consider a 100 horsepower (HP) compressor operating for 8,000 hours per year. A fixed speed compressor in this scenario would consume approximately 750,000 kWh of electricity annually. If a variable speed compressor reduces energy consumption by 30%, it would save 225,000 kWh per year. Using the U.S. Environmental Protection Agency’s greenhouse gas equivalencies calculator, this energy savings equates to:
- Greenhouse gas emissions from 34.2 passenger vehicles driven for one year
- CO2 emissions from 18.9 homes’ electricity use for one year
- Carbon sequestered by 3,719 tree seedlings grown for 10 years
By reducing energy consumption and the associated greenhouse gas emissions, variable speed compressors contribute to a company’s sustainability efforts and help mitigate the environmental impact of industrial operations.
Reduced Waste and Increased Lifespan:
The soft start and stop capabilities of variable speed compressors reduce mechanical stress on components, extending their lifespan and minimizing the need for frequent replacements. This not only saves on maintenance costs but also reduces waste generated from worn-out parts and components.
Additionally, the precise pressure control of variable speed compressors helps maintain consistent air quality, reducing the risk of moisture, oil, or particulate contamination in the compressed air supply. This can lead to improved product quality, reduced scrap rates, and minimized waste in downstream processes.
Compliance with Environmental Regulations:
Many countries and regions have implemented strict environmental regulations and energy efficiency standards for industrial equipment, including compressed air systems. Variable speed compressors, with their energy-saving capabilities, can help businesses comply with these regulations and avoid potential penalties or fines.
Green Building Certifications:
Businesses seeking green building certifications, such as LEED (Leadership in Energy and Environmental Design) or BREEAM (Building Research Establishment Environmental Assessment Method), can benefit from incorporating variable speed compressors into their facilities. These certifications recognize and reward sustainable building practices, including energy-efficient equipment and systems.
By installing variable speed compressors and demonstrating their energy savings, companies can earn points towards these certifications, enhancing their environmental credentials and potentially attracting environmentally conscious customers and investors.
In conclusion, variable speed compressors offer a more environmentally friendly solution for compressed air systems compared to fixed speed compressors. Their energy efficiency, reduced waste, and compliance with environmental regulations make them an attractive choice for businesses looking to minimize their environmental impact and promote sustainable practices.
Frequently Asked Questions
Q1: What are the main advantages of a variable speed air compressor?
A1: The main advantages of variable speed air compressors include:
- Energy efficiency: By matching motor speed to air demand, variable speed compressors can reduce energy consumption by up to 50% compared to fixed speed compressors.
- Reduced operational costs: The energy savings achieved by variable speed compressors translate into lower operating costs, with potential savings of 30-50% on energy bills.
- Enhanced system reliability: The soft start and stop capabilities of variable speed compressors reduce mechanical stress on components, extending their lifespan and minimizing maintenance requirements.
- Improved air quality: Advanced control systems in variable speed compressors optimize the performance of air treatment components, ensuring consistent air quality and reducing the risk of contamination.
- Environmental benefits: The energy efficiency of variable speed compressors reduces greenhouse gas emissions and contributes to a company’s sustainability goals.
Q2: Can fixed speed compressors be used in any industrial environment?
A2: While fixed speed compressors are versatile and can be used in a wide range of industrial applications, they are best suited for environments with consistent air demand. In applications where the air demand is relatively stable, fixed speed compressors can operate efficiently at their designed capacity without the need for variable speed control.
However, in applications with fluctuating air demand, fixed speed compressors may experience frequent load/unload cycles, leading to increased energy consumption and wear on components. In these scenarios, variable speed compressors are generally more efficient and cost-effective in the long run.
It’s essential to assess your specific application requirements, including the air demand profile, energy costs, and maintenance needs, to determine whether a fixed speed compressor is suitable for your industrial environment.
Q3: How do I decide between variable and fixed speed compressors?
A3: When deciding between variable and fixed speed compressors, consider the following factors:
- Air demand variability: Assess the fluctuations in your air demand over time. If your air demand varies significantly, a variable speed compressor can provide substantial energy savings and operational benefits. If your air demand is relatively constant, a fixed speed compressor may be a cost-effective choice.
- Energy consumption goals: Evaluate your company’s energy efficiency targets and sustainability objectives. Variable speed compressors can significantly reduce energy consumption and greenhouse gas emissions, aligning with corporate environmental initiatives.
- Budget and long-term costs: Consider both the initial investment and the long-term operating costs. Variable speed compressors typically have a higher upfront cost but can offer significant energy savings over time, resulting in a lower total cost of ownership. Fixed speed compressors may have a lower initial cost but may be less energy-efficient in the long run.
- Maintenance requirements: Assess your in-house maintenance capabilities and the availability of skilled technicians. Fixed speed compressors generally require less specialized maintenance compared to variable speed compressors, which may be a consideration for facilities with limited technical resources.
- Future growth and scalability: Evaluate your current facility size and potential expansion plans. Variable speed compressors offer greater flexibility and can adapt to changes in air demand as your business grows, while fixed speed compressors may be suitable for smaller facilities with stable air requirements.
Conducting a thorough analysis of your compressed air system, including an air audit and consultation with compressed air experts, can help you make an informed decision based on your unique needs and priorities.
Learn more about the technical aspects of air compressors.
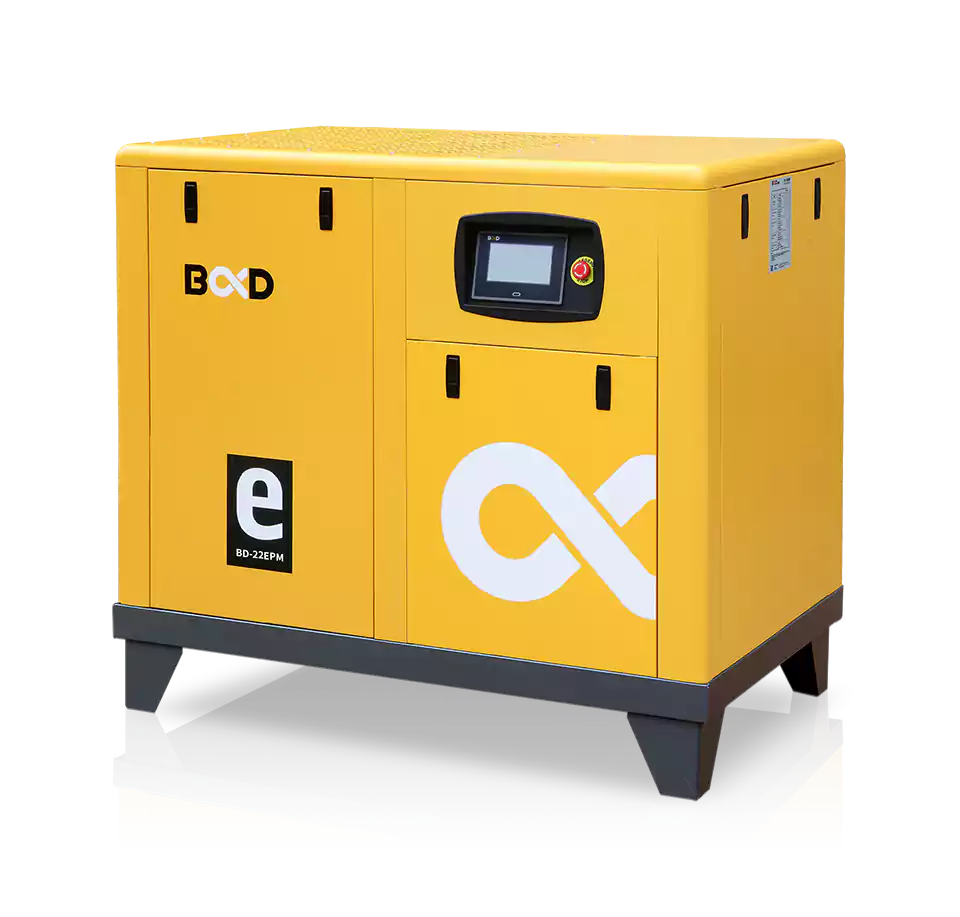
Meta Description: Explore the differences between variable and fixed speed air compressors. Learn about their mechanisms, advantages, and how to choose the right one for your needs, with insights into energy efficiency and operational stability to make an informed decision.