Introduction to Rotary Screw Air Compressors
Rotary screw air compressors are a critical component for various applications, ranging from industrial environments to service vehicles. This guide explores the intricate workings of rotary screw air compressors, their advantages, types, and the considerations for selecting the right compressor for your needs.
Rotary screw compressors have become increasingly popular in recent years due to their efficiency, reliability, and versatility. They are designed to provide a continuous flow of compressed air, making them ideal for applications that require a constant supply of air, such as manufacturing plants, automotive shops, and construction sites.
One of the key advantages of rotary screw compressors is their ability to operate at high speeds and deliver large volumes of compressed air. This is achieved through the use of two meshing helical rotors, which compress the air as it moves through the compressor. The rotors are precision-engineered to ensure optimal performance and durability.
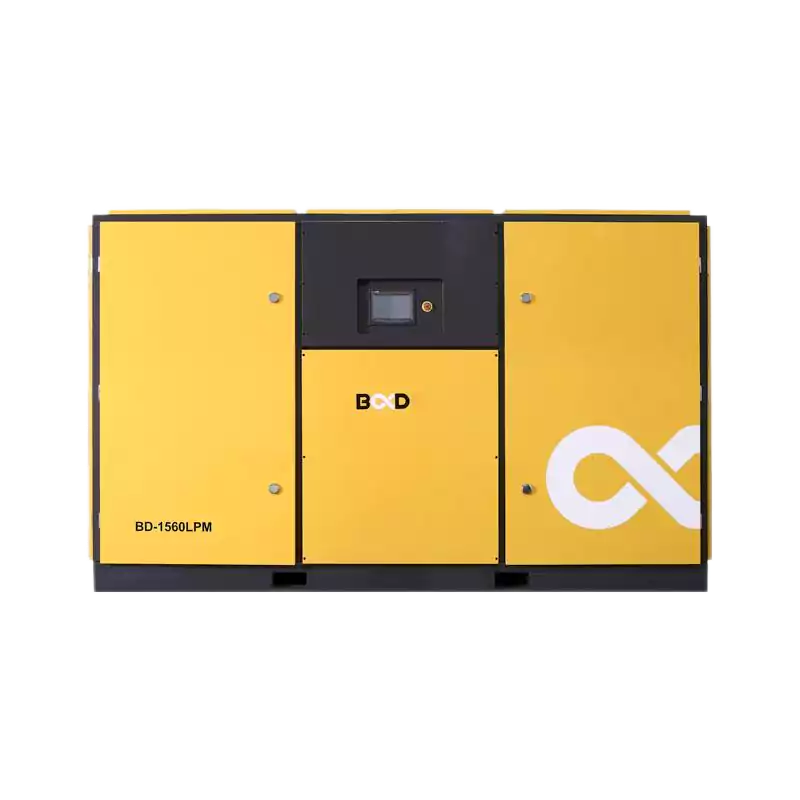
In addition to their performance capabilities, rotary screw compressors are also known for their energy efficiency. Many models feature variable speed drives, which allow the compressor to adjust its output based on the demand for compressed air. This helps to reduce energy consumption and operating costs, making rotary screw compressors an economical choice for businesses of all sizes.
Whether you’re a small workshop owner or a large industrial facility manager, understanding the fundamentals of rotary screw air compressors is essential for making informed decisions about your compressed air needs. In the following sections, we’ll delve deeper into the workings of these compressors, explore the different types available, and provide guidance on selecting the right model for your specific application.
Understanding How Rotary Screw Compressors Work
Rotary screw air compressors operate by drawing air between two meshed rotors, compressing it as the volume decreases along the rotors’ path. This method is highly efficient, providing continuous compressed air, unlike other types that may require intervals of downtime. Learn more about the operation and benefits in the “How Does A Rotary Screw Compressor Work?” article.
The compression process in a rotary screw compressor involves several key components:
- Inlet valve: This valve controls the flow of air into the compressor. As the rotors turn, the inlet valve opens, allowing air to enter the compression chamber.
- Rotors: The heart of the rotary screw compressor is the pair of helical rotors. One rotor, known as the male rotor, features convex lobes, while the other, the female rotor, has concave flutes. As the rotors mesh together, they create a series of decreasing volume pockets that compress the air.
- Compression chamber: The compression chamber houses the rotors and is where the actual compression takes place. As the rotors turn, the air is progressively compressed as it moves from the inlet side to the discharge side.
- Discharge port: Once the air reaches the end of the rotors, it is fully compressed and ready to be discharged from the compressor. The discharge port directs the compressed air into the storage tank or directly to the point of use.
- Cooling system: Compressing air generates heat, which must be dissipated to maintain optimal performance and prevent damage to the compressor. Rotary screw compressors typically feature an integrated cooling system, which may include an oil cooler, air cooler, or a combination of both.
The continuous compression process of rotary screw compressors offers several advantages over other types of compressors. First, it provides a steady flow of compressed air without the pulsation that can occur with reciprocating compressors. This is particularly beneficial for applications that require a consistent air supply, such as pneumatic tools or automated equipment.
Second, rotary screw compressors are capable of operating at 100% duty cycle, meaning they can run continuously without the need for downtime. This is in contrast to reciprocating compressors, which typically have a duty cycle of around 50-60%. The ability to run continuously makes rotary screw compressors ideal for demanding industrial applications where downtime can be costly.
Finally, rotary screw compressors are generally more energy-efficient than other types of compressors. The continuous compression process and the ability to adjust output based on demand help to minimize energy waste and reduce operating costs.
Understanding how rotary screw compressors work is essential for selecting the right compressor for your needs and ensuring optimal performance. By familiarizing yourself with the key components and the compression process, you’ll be better equipped to make informed decisions about your compressed air system.
Choosing the Right Compressor
Selecting the right air compressor involves understanding your specific air delivery needs and the environment in which the compressor will operate. Whether for industrial use or service vehicles, factors like compressor size, power source, and whether you need an oil-injected or oil-free system play crucial roles. For detailed guidance, see “How to choose the right rotary screw compressor”.
When choosing a rotary screw air compressor, there are several key factors to consider:
- Air demand: The first step in selecting the right compressor is to determine your air demand. This involves calculating the total air consumption of all the tools and equipment that will be connected to the compressor. It’s important to consider not only the average air demand but also peak demand to ensure the compressor can meet your needs during periods of high usage.
- Pressure requirements: Different applications require different pressure levels. For example, pneumatic tools typically require pressures between 90 and 120 PSI, while some industrial processes may require higher pressures. Make sure to choose a compressor that can deliver the necessary pressure for your specific application.
- Power source: Rotary screw compressors can be powered by electricity or diesel engines. Electric compressors are more common in stationary applications, while diesel-powered compressors are often used in mobile or remote applications where electricity may not be readily available.
- Oil-injected vs. oil-free: Rotary screw compressors are available in both oil-injected and oil-free configurations. Oil-injected compressors use oil to lubricate and cool the rotors, while oil-free compressors use special coatings and seals to prevent oil contamination. Oil-free compressors are necessary for applications where air purity is critical, such as food processing or pharmaceutical manufacturing.
- Cooling method: Rotary screw compressors generate heat during operation, which must be dissipated to prevent damage and ensure optimal performance. There are two primary cooling methods: air-cooled and water-cooled. Air-cooled compressors use fans to blow air over the compressor components, while water-cooled compressors use a water-cooling system to remove heat. The choice between air-cooled and water-cooled depends on factors such as ambient temperature, available space, and water supply.
- Maintenance requirements: Regular maintenance is essential for ensuring the longevity and reliability of your rotary screw compressor. When selecting a compressor, consider the maintenance requirements, including the frequency of oil changes, filter replacements, and other routine tasks. Some compressors feature extended maintenance intervals or easy-access designs that simplify maintenance tasks.
- Noise level: Rotary screw compressors are generally quieter than reciprocating compressors, but noise levels can still vary between models. If your compressor will be located in a noise-sensitive environment, such as a medical facility or office building, look for models with low noise levels or sound-attenuating enclosures.
- Energy efficiency: Compressed air is one of the most expensive utilities in many industrial facilities, so energy efficiency is a critical consideration when selecting a rotary screw compressor. Look for models with variable speed drives, which can adjust the compressor output based on demand, reducing energy consumption during periods of low usage. Also, consider the specific power consumption of the compressor, which measures the amount of energy required to produce a given volume of compressed air.
By carefully evaluating these factors and consulting with a compressed air professional, you can select a rotary screw compressor that meets your specific needs and provides reliable, efficient performance for years to come.
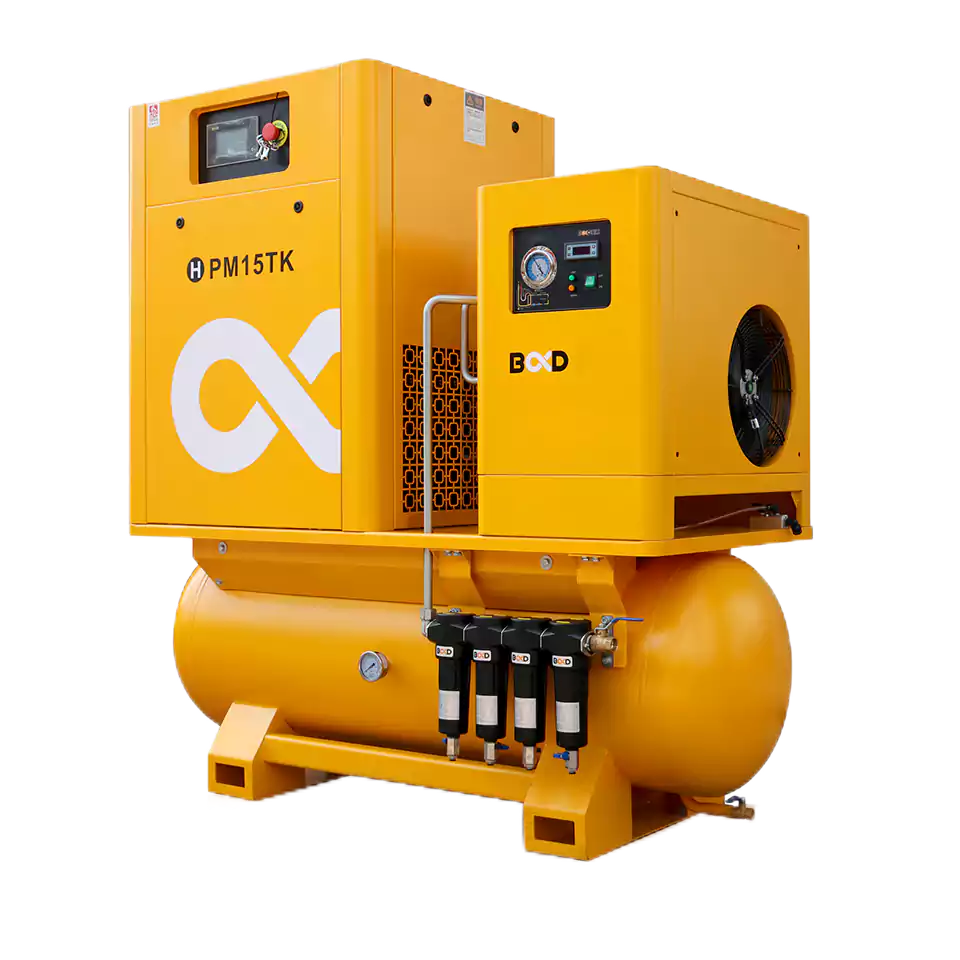
Types of Rotary Screw Compressors
Up to 30 HP Models
Smaller rotary screw compressors, suitable for compact setups and lower power requirements, offer versatility without sacrificing performance. These models are ideal for applications requiring up to 30 horsepower. Discover specific models suited for various applications at “Rotary screw compressors up to 30 hp”.
Rotary screw compressors in the up to 30 HP range are well-suited for a variety of small to medium-sized applications, such as:
- Auto repair shops: These compressors can power pneumatic tools, spray painting equipment, and tire inflation systems.
- Woodworking shops: Rotary screw compressors provide a reliable air supply for sanders, nailers, and other woodworking tools.
- Machine shops: Smaller machine shops can benefit from the consistent air supply and low maintenance requirements of rotary screw compressors.
- Dental and medical practices: Oil-free rotary screw compressors are ideal for dental and medical applications where air purity is critical.
When selecting a rotary screw compressor in this size range, consider factors such as:
- Air demand: Calculate the total air consumption of your tools and equipment to ensure the compressor can meet your needs.
- Power requirements: Make sure your electrical supply can support the compressor’s power requirements.
- Noise level: If the compressor will be located in a noise-sensitive area, look for models with low noise levels or sound-attenuating enclosures.
- Maintenance requirements: Consider the frequency of oil changes, filter replacements, and other routine maintenance tasks.
Some notable rotary screw compressors in the up to 30 HP range include:
- Kaeser SM series: These compact, energy-efficient compressors feature Sigma Profile airends and integrated dryers for superior performance and air quality.
- Atlas Copco GA series: The GA series offers reliable, efficient performance with low noise levels and easy maintenance access.
- Sullair ShopTek series: Designed for small shops and businesses, ShopTek compressors provide a dependable air supply with low operating costs.
- B&D EPM series: These variable speed drive compressors feature a highly efficient PM motor and advanced PLC control system for optimal energy savings and performance. The EPM series delivers reliable, quiet operation in a compact footprint.
By carefully evaluating your needs and selecting a high-quality rotary screw compressor in the up to 30 HP range, you can ensure a reliable, efficient compressed air supply for your small to medium-sized application.
Variable Speed Drive Compressors
Variable speed drive (VSD) compressors adjust their motor speed to match the air demand, significantly enhancing energy efficiency. This feature is particularly useful in applications with fluctuating air use. Learn more about VSD compressors at “Screw Compressors – ABAC Air Compressors International”.
Variable speed drive (VSD) compressors are an increasingly popular choice for businesses looking to reduce energy costs and improve efficiency. These compressors use advanced electronic controls to adjust the motor speed based on the air demand, ensuring that the compressor only produces the amount of air needed at any given time.
The benefits of VSD compressors include:
- Energy savings: By matching the compressor output to the air demand, VSD compressors can reduce energy consumption by up to 50% compared to fixed-speed compressors.
- Reduced wear and tear: VSD compressors eliminate the frequent starting and stopping associated with fixed-speed compressors, reducing wear on the motor and other components.
- Improved air quality: VSD compressors maintain a more consistent pressure level, which can help improve air quality by reducing moisture and contaminants.
- Quieter operation: The variable speed motor in VSD compressors runs at lower speeds during periods of low demand, resulting in quieter operation.
When considering a VSD compressor, it’s important to evaluate your air demand profile. VSD compressors are most effective in applications with variable air demand, such as:
- Manufacturing plants with multiple shifts or varying production levels
- Facilities with seasonal or intermittent air usage
- Businesses with multiple air-using processes that operate at different times
To maximize the benefits of a VSD compressor, it’s important to properly size the compressor based on your air demand and pressure requirements. A compressed air professional can help you evaluate your needs and select the right VSD compressor for your application.
Some notable VSD rotary screw compressors include:
- Atlas Copco GA VSD+ series: These compressors feature advanced VSD technology and a unique motor design for optimal efficiency and reliability.
- Kaeser Sigma Frequency Control (SFC) series: Kaeser’s SFC compressors combine VSD technology with the energy-efficient Sigma Profile airend for maximum performance and savings.
- Ingersoll Rand Nirvana VSD series: The Nirvana series offers a wide range of VSD compressors with advanced controls and remote monitoring capabilities.
- F18AIR PM series: Designed for demanding industrial applications, the F18AIR PM series combines a high-efficiency permanent magnet motor with a robust airend for superior performance and reliability. These variable speed drive compressors offer significant energy savings and low noise levels.
By investing in a VSD rotary screw compressor, businesses can reduce energy costs, improve air quality, and enhance the overall efficiency of their compressed air system.
Industrial and Service Vehicle Compressors
For larger, more demanding environments such as factories or mobile service units, industrial air compressors and those designed specifically for service vehicles offer robust solutions. These compressors ensure reliability and efficiency under tough conditions. Explore the options detailed in the “Easy Guide To Rotary Screw Air Compressors – 2024 Edition”.
Industrial and service vehicle rotary screw compressors are designed to withstand the rigors of demanding applications and harsh environments. These compressors offer the reliability, durability, and performance needed to keep operations running smoothly and efficiently.
Industrial rotary screw compressors are typically larger and more powerful than their smaller counterparts, with capacities ranging from 30 HP to over 500 HP. They are designed for continuous operation and can handle the the high air demands of large manufacturing plants, processing facilities, and other industrial applications.
Key features of service vehicle rotary screw compressors include:
- Compact and lightweight design: Service vehicle compressors are designed to fit in the limited space available on trucks and vans, while minimizing weight to reduce fuel consumption and maintain vehicle handling.
- Reliable performance: These compressors are built to withstand the vibration, shock, and environmental conditions encountered in mobile applications, ensuring reliable operation in the field.
- Versatile mounting options: Service vehicle compressors can be mounted in various configurations, such as underhood, underdecks, or side-mount installations, depending on the available space and accessibility requirements.
- Power options: Service vehicle compressors are available with various power options to match the vehicle’s electrical system, including 12V or 24V DC power, hydraulic power, or power takeoff (PTO) driven systems.
- Integrated air management: Many service vehicle compressors feature integrated air management systems, including air dryers, filters, and regulators, to ensure a clean, dry, and stable compressed air supply for tools and equipment.
Some notable industrial and service vehicle rotary screw compressors include:
- Sullair 1600H AF: This portable, diesel-driven compressor delivers up to 1,600 cfm at 100 psi, making it ideal for demanding industrial applications and remote worksites.
- Kaeser M114: A compact, efficient compressor designed for service vehicles, the M114 delivers up to 110 cfm at 100 psi and features a lightweight, corrosion-resistant design.
- VMAC G30: This gas-powered, underhood compressor delivers up to 30 cfm at 100 psi and is designed for light-duty service trucks and vans.
- B&D LPM series: The LPM series of low-pressure rotary screw compressors is ideal for applications requiring large volumes of air at lower pressures. Its low rotating speed helps ensure energy efficiency and reduced noise levels, while still maintaining a good free air delivery volume for long-term operation.
By selecting the right industrial or service vehicle rotary screw compressor for your application, you can ensure a reliable, efficient compressed air supply for your most demanding projects, whether in the factory or on the job site.
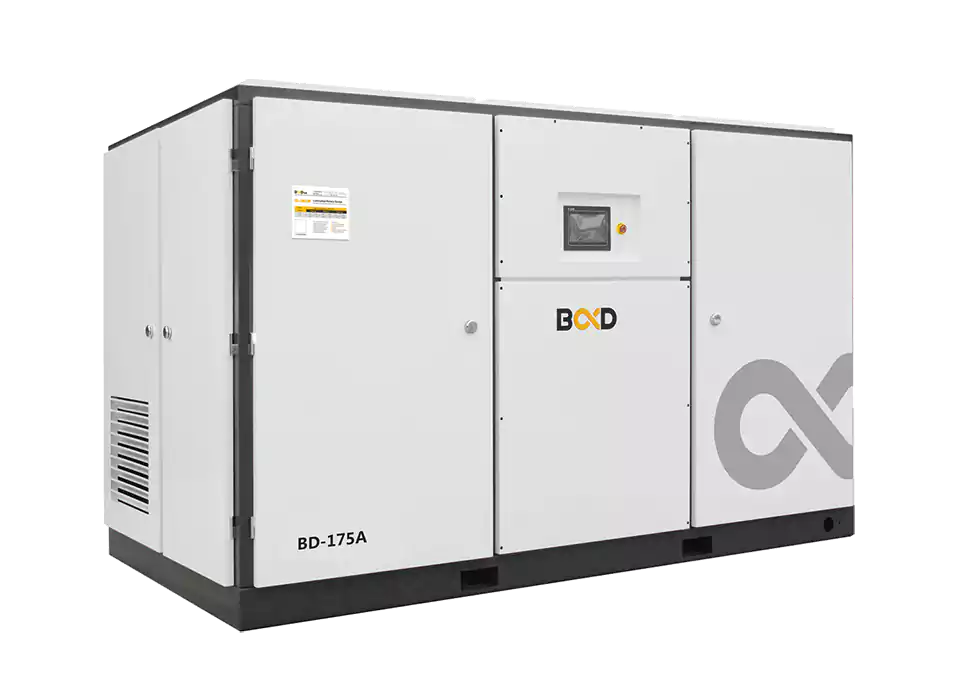
Maintenance and Reliability
To maximize the lifespan and efficiency of rotary screw compressors, regular maintenance is crucial. This includes routine checks and replacing oil, filters, and separators to prevent breakdowns and ensure consistent performance.
Proper maintenance is essential for ensuring the reliability and longevity of your rotary screw air compressor. By following a regular maintenance schedule and addressing potential issues promptly, you can minimize downtime, reduce repair costs, and extend the life of your compressor.
Some key maintenance tasks for rotary screw compressors include:
- Oil changes: Regularly changing the compressor oil is critical for maintaining optimal performance and preventing wear on internal components. The frequency of oil changes depends on factors such as the compressor’s operating hours, the type of oil used, and the environment in which the compressor operates. Consult your compressor’s manual or a compressed air professional for guidance on the appropriate oil change interval.
- Filter replacements: Rotary screw compressors typically have several filters, including air intake filters, oil filters, and air/oil separator elements. These filters remove contaminants from the air and oil, protecting the compressor’s internal components and ensuring clean, high-quality compressed air. Replace filters according to the manufacturer’s recommendations or when they become visibly dirty or clogged.
- Cooler cleaning: The air and oil coolers in rotary screw compressors dissipate heat generated during the compression process. Over time, dust and debris can accumulate on the cooler fins, reducing their efficiency and potentially causing overheating. Regularly clean the cooler fins to maintain proper heat dissipation and prevent damage to the compressor.
- Belt tensioning and replacement: For belt-driven rotary screw compressors, it’s important to maintain proper belt tension and replace belts when they show signs of wear. Loose or worn belts can slip, reducing efficiency and potentially causing damage to the compressor. Check belt tension regularly and replace belts according to the manufacturer’s recommendations.
- Leak detection and repair: Compressed air leaks can significantly reduce the efficiency of your compressed air system and increase energy costs. Regularly inspect your compressed air lines, fittings, and connections for leaks, and repair them promptly. Ultrasonic leak detectors can help identify leaks that may not be audible or visible.
In addition to these routine maintenance tasks, it’s important to keep detailed records of all maintenance activities and compressor performance data. This information can help you identify trends, anticipate potential issues, and make informed decisions about repairs or replacements.
By prioritizing maintenance and addressing potential issues promptly, you can ensure the reliability and efficiency of your rotary screw air compressor, minimizing downtime and maximizing the return on your investment.
Power Transmission and Efficiency
Effective power transmission is key to maximizing the efficiency of rotary screw compressors. Systems with direct drive or gear drive often offer better power transmission compared to belt-driven systems, which can slip and reduce efficiency over time.
Power transmission is a critical factor in the efficiency and performance of rotary screw air compressors. The method by which power is transferred from the motor to the compressor’s airend can significantly impact energy consumption, reliability, and maintenance requirements.
There are three primary power transmission methods used in rotary screw compressors:
- Direct drive: In a direct drive system, the motor is directly coupled to the compressor airend, eliminating the need for belts or gears. This configuration offers several advantages, including:
- High efficiency: Direct drive systems minimize power transmission losses, resulting in higher overall efficiency compared to belt-driven or gear-driven systems.
- Compact design: The direct coupling of the motor and airend allows for a more compact compressor design, saving valuable floor space.
- Low maintenance: With fewer moving parts, direct drive systems require less maintenance than belt-driven or gear-driven systems.
- Gear drive: Gear-driven rotary screw compressors use a gearbox to transfer power from the motor to the airend. This configuration offers some advantages over belt-driven systems, such as:
- Improved efficiency: Gear drive systems typically have lower power transmission losses compared to belt-driven systems, resulting in higher efficiency.
- Longer service life: Gears are more durable than belts and can last longer, reducing maintenance costs over the life of the compressor.
- Belt drive: Belt-driven rotary screw compressors use belts and pulleys to transfer power from the motor to the airend. While belt-driven systems are generally less efficient than direct drive or gear drive systems, they offer some advantages, including:
- Lower initial cost: Belt-driven compressors are often less expensive than direct drive or gear drive systems, making them a more affordable option for some applications.
- Flexibility: Belt-driven systems allow for more flexibility in the placement of the motor and airend, which can be advantageous in certain installations.
When selecting a rotary screw compressor, it’s important to consider the power transmission method and its impact on efficiency, reliability, and maintenance requirements. While direct drive and gear drive systems offer higher efficiency and lower maintenance costs, belt-driven systems may be a more affordable option for some applications.
Regardless of the power transmission method, proper maintenance is essential for ensuring optimal performance and efficiency. This includes regular belt tensioning and replacement for belt-driven systems, as well as oil changes and other routine maintenance tasks for all types of rotary screw compressors.
By understanding the advantages and limitations of each power transmission method and prioritizing regular maintenance, you can maximize the efficiency and reliability of your rotary screw air compressor, ensuring a dependable and cost-effective compressed air supply for your application.
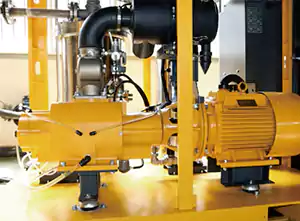
Frequently Asked Questions
What are the advantages of using rotary screw air compressors?
Rotary screw compressors provide continuous airflow and are more energy-efficient, making them ideal for high-demand applications. Some key advantages of rotary screw compressors include:
- Continuous air supply: Rotary screw compressors provide a constant flow of compressed air, without the pulsation that can occur with reciprocating compressors. This makes them ideal for applications that require a steady air supply, such as pneumatic tools or automated equipment.
- High efficiency: The continuous compression process and the ability to adjust output based on demand help to minimize energy waste and reduce operating costs. Many rotary screw compressors also feature variable speed drives, which further enhance energy efficiency.
- Durability and reliability: Rotary screw compressors are designed for continuous operation and can run at 100% duty cycle without the need for downtime. They are built with durable components and rugged enclosures to withstand demanding industrial environments.
- Low noise levels: Rotary screw compressors are generally quieter than reciprocating compressors, making them suitable for use in noise-sensitive environments such as medical facilities or office buildings.
- Customizable configurations: Rotary screw compressors can be customized with a variety of options, such as integrated dryers, filters, and control systems, to meet the specific needs of each application.
By offering a combination of continuous air supply, high efficiency, durability, low noise levels, and customizable configurations, rotary screw compressors provide a versatile and reliable compressed air solution for a wide range of applications.
Can rotary screw compressors be used in mobile applications?
Yes, certain models are specifically designed for mobile applications, offering compact, robust solutions for service vehicles. These compressors are engineered to withstand the rigors of mobile use and provide a dependable compressed air supply for on-site work.
Some key features of rotary screw compressors designed for mobile applications include:
- Compact and lightweight design: Mobile compressors are designed to fit in the limited space available on service vehicles, such as utility trucks and vans. They feature compact, lightweight construction to maximize payload capacity and minimize the impact on vehicle handling.
- Rugged construction: Mobile compressors are built to withstand the vibration, shock, and environmental conditions encountered in mobile applications. They feature durable components, heavy-duty enclosures, and vibration isolation to ensure reliable operation in challenging conditions.
- Versatile mounting options: Mobile compressors can be mounted in various configurations to suit the specific needs of each vehicle and application. This may include underhood, underdecks, or side-mount installations, depending on the available space and accessibility requirements.
- Power options: Mobile compressors are available with various power options to match the electrical system of the vehicle. This may include 12V or 24V DC power, hydraulic power, or power takeoff (PTO) driven systems.
- Integrated air management: Many mobile compressors feature integrated air management systems, including air dryers, filters, and regulators, to ensure a clean, dry, and stable compressed air supply for tools and equipment.
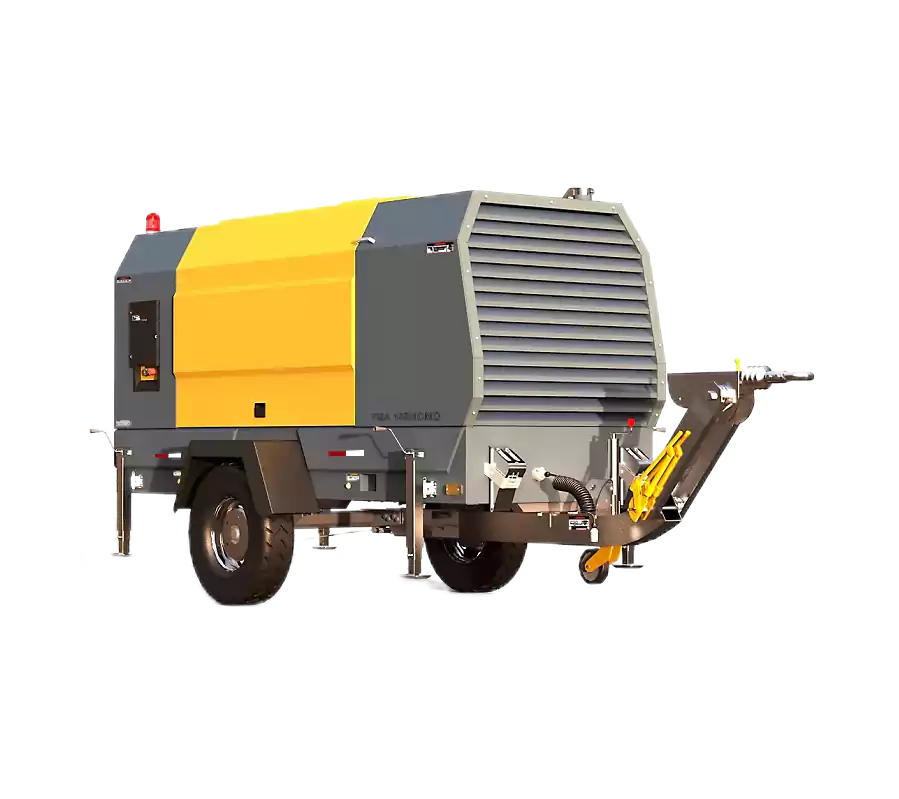
By offering compact, rugged, and versatile designs, rotary screw compressors designed for mobile applications provide a reliable and efficient compressed air solution for service vehicles and other mobile worksite needs.
What is the difference between oil-injected and oil-free compressors?
Oil-injected compressors use oil to lubricate moving parts, which is ideal for general industrial use, whereas oil-free compressors are necessary for applications where air purity is critical, such as in medical or food processing environments.
The main difference between oil-injected and oil-free rotary screw compressors lies in how the compressor lubricates and cools its internal components:
- Oil-injected compressors: In an oil-injected rotary screw compressor, oil is injected into the compression chamber to lubricate and cool the rotors. The oil forms a seal between the rotors, helping to improve efficiency and reduce wear. After the compression process, the oil is separated from the compressed air using an oil separator, and the air is then cooled and filtered before being discharged.Advantages of oil-injected compressors:
- Lower initial cost compared to oil-free compressors
- Higher efficiency due to the cooling and sealing effects of the oil
- Longer service life and lower maintenance costs
Disadvantages of oil-injected compressors:
- Potential for oil contamination in the compressed air, which may not be suitable for certain applications
- Requires regular oil changes and oil filter replacements
- Oil-free compressors: Oil-free rotary screw compressors use special coatings and seals on the rotors to prevent oil from entering the compression chamber. The rotors are designed to operate without lubrication, and the compressed air is cooled using an external cooling system, such as air or water cooling.Advantages of oil-free compressors:
- 100% oil-free compressed air, which is essential for applications where air purity is critical, such as food processing, pharmaceuticals, or electronics manufacturing
- Eliminates the need for oil changes and oil filter replacements
- Reduces the risk of contamination and associated product spoilage or recalls
Disadvantages of oil-free compressors:
- Higher initial cost compared to oil-injected compressors
- Lower efficiency due to the absence of oil cooling and sealing
- May require more frequent maintenance of the air-end due to the lack of lubrication
When choosing between an oil-injected and an oil-free rotary screw compressor, consider the specific requirements of your application, including air purity needs, budget, and maintenance preferences. For general industrial use, oil-injected compressors offer a cost-effective and efficient solution. However, for applications where air purity is critical, oil-free compressors are the necessary choice to ensure contaminant-free compressed air.
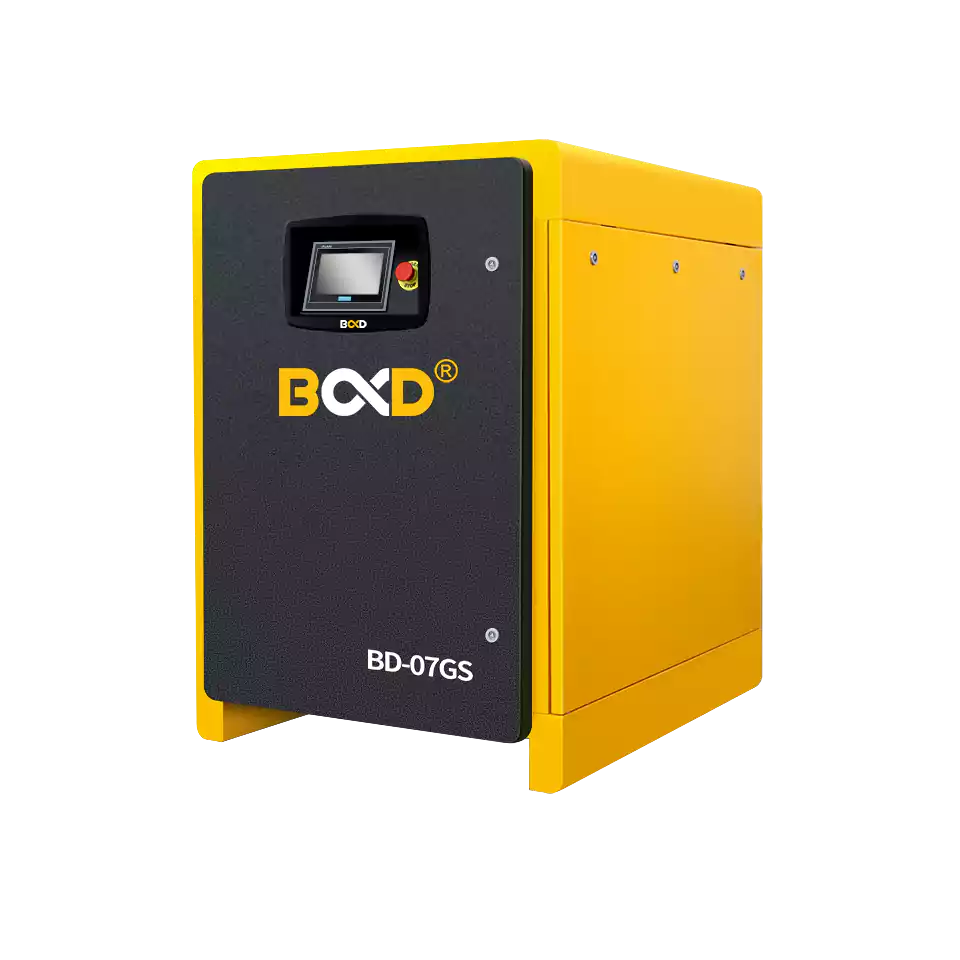
Meta Description: Explore our comprehensive guide on rotary screw air compressors, covering everything from basic operations and types to efficiency tips and selection guidelines for industrial and service vehicle applications. Dive into detailed insights and make an informed choice with expert advice.