Understanding the differences between rotary screw and reciprocating compressors is crucial for selecting the right compressor for your needs. Each type has its distinct advantages and applications, influenced by their design, performance, and efficiency.
Key Differences Between Rotary Screw and Reciprocating Compressors
The fundamental difference between rotary screw and reciprocating compressors lies in their compression mechanics.Rotary screw compressors utilize two interlocking helical screws to compress air continuously, while reciprocating compressors employ a piston-driven mechanism to compress air in a back-and-forth motion.
Compression Mechanics and Efficiency
Rotary screw compressors operate on a principle of two interlocking helical screws that compress the air as they rotate, which provides a continuous flow of compressed air with minimal pulsations. This design not only enhances the efficiency but also reduces the energy loss commonly associated with reciprocating compressors.
On the other hand, reciprocating compressors utilize a piston mechanism that compresses air in a back-and-forth motion, which is more suitable for applications requiring intermittent air supply. The Atlas Copco guide highlights that although less efficient in continuous use, they are highly effective for lower volume requirements.
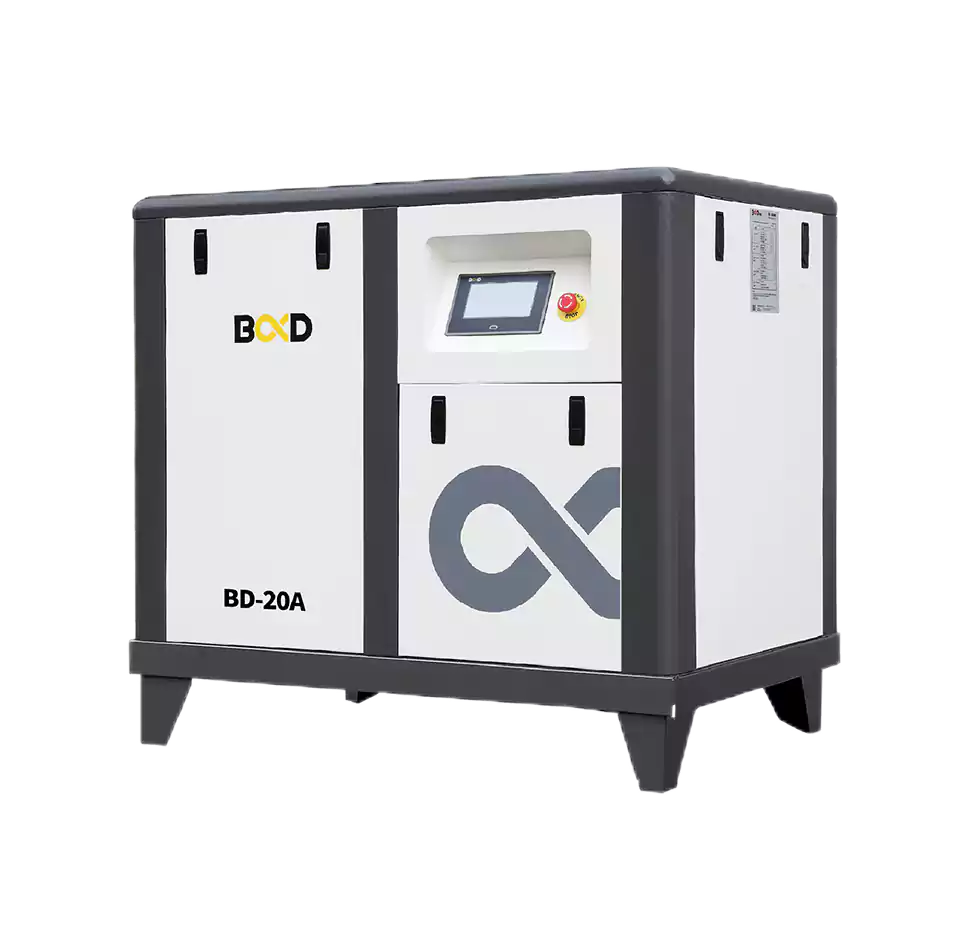
Maintenance and Operational Demands
Rotary screw compressors are known for their durability and longer operational life, requiring less frequent maintenance compared to reciprocating compressors. They are ideal for demanding industrial environments where air supply needs are constant and high.
In contrast, reciprocating compressors, while generally more affordable upfront, involve higher maintenance due to their many moving parts and wear from the reciprocating action, as detailed by Lewis Systems Inc.
Performance Under Different Conditions
Rotary screw compressors excel in applications that require a continuous, high-volume supply of compressed air. Their high-duty cycle and ability to operate efficiently under demanding conditions make them suitable for manufacturing, industrial processes, and large-scale operations.
Reciprocating compressors, on the other hand, are better suited for intermittent use and applications where air demand fluctuates. They perform well in environments that require occasional bursts of compressed air, such as automotive workshops, construction sites, and smaller facilities.
The choice between these two types of compressors often comes down to their performance under specific operational conditions.Rotary screw compressors offer a high-duty cycle, suitable for high-pressure applications and continuous operation. Reciprocating compressors perform better in environments where usage is less frequent and air demand fluctuates.
Selecting the Right Compressor for Your Needs
Choosing the right compressor depends on various factors, including the application, air demand, operating conditions, and budget. It is essential to assess your specific requirements and consult with compressed air experts to determine the most suitable compressor type for your needs.
Considerations for Industrial Use
For industrial applications, the suitability of rotary screw compressors is often unmatched due to their ability to operate 24/7 with high reliability and low energy consumption. Their robust design allows them to handle larger volumes of air efficiently, making them a staple in manufacturing and production settings.
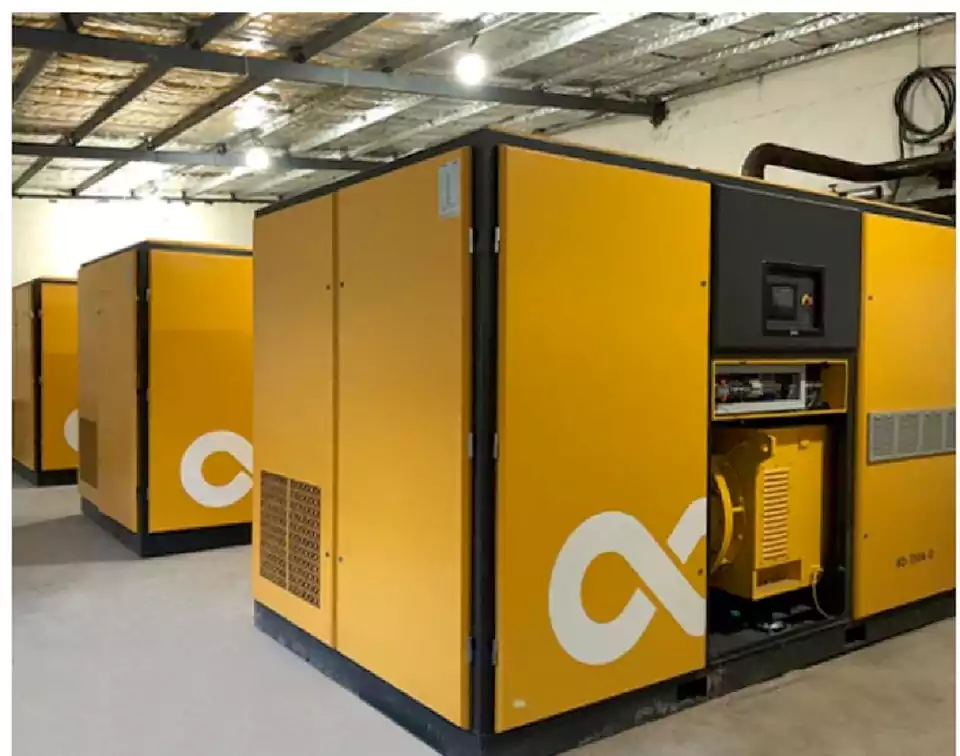
Small-Scale and Intermittent Applications
For smaller or less frequent applications, reciprocating compressors are more appropriate. They offer flexibility and are easier to install and maintain on a smaller scale, as noted in the BAC Compressors guide.
Frequently Asked Questions
What are the primary advantages of rotary screw compressors?
Rotary screw compressors are favored for their efficiency, continuous air production, and lower operational noise, making them ideal for heavy-duty industrial use. Their robust design, fewer moving parts, and longer service life contribute to their popularity in demanding applications.
How do reciprocating compressors compare in terms of cost?
Reciprocating compressors generally have a lower initial cost but may incur higher maintenance expenses and energy costs in the long run, particularly at higher CFM levels. However, they remain a cost-effective choice for smaller-scale and intermittent applications.
Which compressor type is more energy-efficient?
Rotary screw compressors are typically more energy-efficient, especially in settings where continuous air supply is required, due to their design and operational mechanics. They consume less energy per unit of compressed air produced compared to reciprocating compressors, resulting in long-term cost savings.
Meta Description:
Explore the differences between rotary screw and reciprocating compressors, including their mechanics, efficiency, maintenance needs, and applications. Understand which compressor type best fits your industrial or intermittent air supply needs.