Understanding the Cubic Feet per Minute (CFM) rating is crucial for selecting and utilizing rotary screw air compressors effectively. This guide provides an in-depth look at the significance of CFM, how to calculate it, and its impact on air compressor performance and efficiency.
What is CFM in Air Compressors?
Defining CFM and its Importance
CFM, or Cubic Feet per Minute, measures the volume of air an air compressor delivers in a minute. It’s a critical factor in determining the suitability of an air compressor for various tools and applications.
CFM directly relates to the power and capability of an air compressor. A higher CFM rating indicates that the compressor can supply a larger volume of air, making it suitable for more demanding applications or running multiple tools simultaneously.
Conversely, a lower CFM rating is better suited for smaller, less air-intensive tasks. It’s essential to match the CFM rating of your air compressor to the requirements of your pneumatic tools.
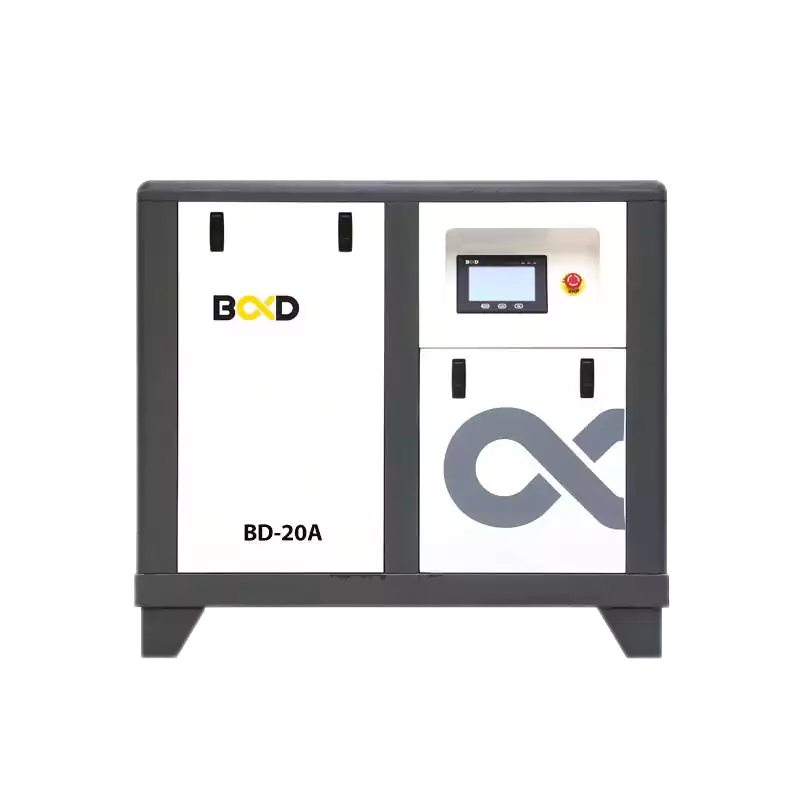
Insufficient CFM can lead to tool performance issues, such as reduced power, stalling, or even damage to the equipment. On the other hand, an excessively high CFM can result in wasted energy and increased operating costs. Learn more about CFM basics from Atlas Copco.
CFM Calculation Explained
Calculating CFM involves assessing the volume of air moved by the compressor at a specific pressure level. This calculation is essential for ensuring that your air compressor can meet the demands of your pneumatic tools efficiently.
The CFM calculation takes into account factors such as the compressor’s displacement (the volume of air moved per revolution), the motor’s speed (revolutions per minute), and the compressor’s volumetric efficiency (the ratio of actual air delivered to the theoretical maximum).
To calculate CFM, you can use the following formula: CFM = (Displacement × RPM × Volumetric Efficiency) / 1728
Where:
- Displacement is measured in cubic inches
- RPM is the motor’s speed in revolutions per minute
- Volumetric Efficiency is expressed as a decimal (e.g., 0.85 for 85%)
- 1728 is a constant to convert cubic inches to cubic feet
For example, if a compressor has a displacement of 100 cubic inches, runs at 1000 RPM, and has a volumetric efficiency of 85%, the CFM calculation would be: CFM = (100 × 1000 × 0.85) / 1728 = 49.2 CFM
VMAC’s guide provides insights into the difference between PSI and CFM, enhancing your understanding of CFM’s role in compressor performance.
Optimizing Air Compressor Performance
Matching CFM with Pneumatic Tool Requirements
Every air tool has a CFM requirement, and it’s crucial to match this with your compressor’s output for optimal performance. Pneumatic tools, such as impact wrenches, grinders, sanders, and spray guns, have specific CFM ratings that indicate the minimum air volume required for proper operation.
These ratings are typically provided by the tool manufacturer and can be found in the product specifications or manual. When selecting an air compressor, it’s essential to consider the highest CFM requirement among your pneumatic tools.
If you plan to run multiple tools simultaneously, you’ll need to add their individual CFM requirements to determine the total CFM needed. It’s also a good practice to add a safety margin of around 30% to account for any leaks or inefficiencies in the compressed air system.
For example, if you have three pneumatic tools with CFM requirements of 5, 8, and 12 respectively, and you plan to run them simultaneously, your total CFM requirement would be: Total CFM = (5 + 8 + 12) × 1.3 = 32.5 CFM
In this case, you would need an air compressor with a CFM rating of at least 32.5 to ensure optimal performance of all three tools.
The Compressed Air Blog offers detailed explanations on CFM and how it correlates with other compressor specifications like PSI and HP.
Strategies for Efficient Air Compressor Use
Understanding the continuous versus intermittent use of air tools can significantly affect your CFM needs. Tools used continuously require compressors with a higher CFM rating to avoid downtime.
Continuous use refers to operating a pneumatic tool without significant breaks, typically for more than a few minutes at a time. In such cases, the air compressor must be able to supply the tool’s CFM requirement consistently.
On the other hand, intermittent use involves operating a tool with frequent breaks or for short durations. In this scenario, a compressor with a slightly lower CFM rating may suffice, as it has time to recover and replenish the air supply between tool operations.
To optimize air compressor efficiency, consider the following strategies:
- Properly size your compressor: Select an air compressor with a CFM rating that matches your maximum tool requirements, with a reasonable safety margin. Avoid oversizing, as it can lead to increased energy consumption and wear on the compressor.
- Minimize leaks: Regularly inspect and repair any leaks in your compressed air system. Leaks can significantly reduce the available CFM and cause the compressor to work harder, leading to increased energy costs and reduced lifespan.
- Use air storage tanks: Incorporating air storage tanks can help buffer the compressed air supply, particularly for intermittent tool use. The tank stores excess compressed air, which can be drawn upon during peak demand periods, reducing the load on the compressor.
- Implement proper maintenance: Regular maintenance, such as replacing air filters, checking oil levels, and cleaning coolers, ensures that your air compressor operates at peak efficiency. A well-maintained compressor will deliver the rated CFM more consistently and reliably.
For more on how to calculate the right CFM for your compressor, check out ELGi’s guide.
CFM in Action: Practical Applications
Air Tool CFM Chart and Selection Guide
Selecting the right air compressor involves knowing the CFM requirements of your air tools. A CFM chart, like the one provided by SGS Engineering, can be an invaluable resource for this purpose.
The chart lists common air tools and their corresponding CFM requirements, making it easy to determine the total CFM needed for your specific application. For example, the chart indicates that a 1/2″ impact wrench requires 5 CFM, while a die grinder needs 8 CFM.
If you plan to use both tools simultaneously, you would need an air compressor with a minimum CFM rating of 13 (5 + 8). When selecting an air compressor based on CFM, consider the following factors:
- Maximum tool CFM requirement: Choose a compressor that can meet the highest CFM demand among your air tools.
- Simultaneous tool use: If you plan to operate multiple tools at the same time, add their individual CFM requirements to determine the total CFM needed.
- Future expansion: Consider any potential future needs for additional or higher-CFM tools, and select a compressor that can accommodate growth.
- Quality and reliability: Invest in a high-quality air compressor from a reputable manufacturer to ensure consistent CFM output and long-term reliability.
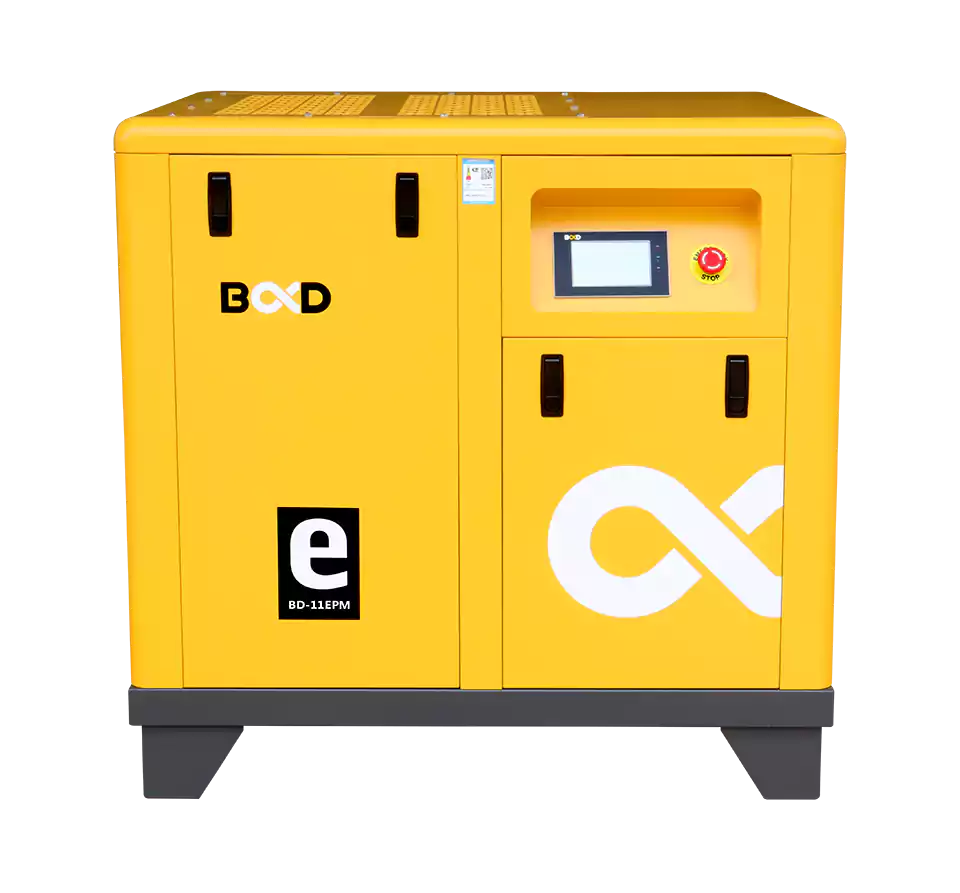
Case Studies: CFM at Work
Real-world examples illustrate how CFM affects air compressor efficiency and performance. Understanding these scenarios can guide you in choosing and using your air compressor more effectively.
Case Study 1: Automotive Workshop An automotive workshop uses a variety of pneumatic tools, including impact wrenches (5 CFM), tire inflators (2 CFM), and spray guns (10 CFM). The workshop operates two impact wrenches and one tire inflator simultaneously, with occasional use of the spray gun.
To calculate the required CFM:
- Continuous use: (2 × 5 CFM for impact wrenches) + (1 × 2 CFM for tire inflator) = 12 CFM
- Intermittent use: 10 CFM for spray gun
The workshop should select an air compressor with a minimum CFM rating of 12 for continuous use, and ensure it can accommodate the additional 10 CFM for intermittent use of the spray gun.
Case Study 2: Woodworking Shop A woodworking shop employs pneumatic sanders (8 CFM), nailers (2 CFM), and staple guns (2 CFM). The shop typically uses one sander and one nailer or staple gun at a time.
To calculate the required CFM:
- Sander: 8 CFM
- Nailer or staple gun: 2 CFM
- Total: 8 + 2 = 10 CFM
The woodworking shop would need an air compressor with a minimum CFM rating of 10 to ensure optimal performance of their tools.
These case studies demonstrate the importance of accurately calculating CFM requirements based on the specific tools and usage patterns in a given application. By selecting an air compressor with the appropriate CFM rating, businesses can ensure efficient operation, minimize downtime, and prolong the life of their pneumatic tools.
Frequently Asked Questions
Q: How do I calculate the CFM for my air compressor?
A: Calculating CFM involves measuring the volume of air your compressor can produce at a given pressure. It’s typically done using a formula that considers the compressor’s size, speed, and efficiency.
The formula for calculating CFM is: CFM = (Displacement × RPM × Volumetric Efficiency) / 1728
Where:
- Displacement is the volume of air moved per revolution, measured in cubic inches
- RPM is the motor’s speed in revolutions per minute
- Volumetric Efficiency is the ratio of actual air delivered to the theoretical maximum, expressed as a decimal
- 1728 is a constant to convert cubic inches to cubic feet
For example, if a compressor has a displacement of 100 cubic inches, runs at 1000 RPM, and has a volumetric efficiency of 85%, the CFM calculation would be: CFM = (100 × 1000 × 0.85) / 1728 = 49.2 CFM
It’s important to note that the actual CFM output may vary slightly from the calculated value due to factors such as air leaks, pressure drops, and environmental conditions. However, this formula provides a good estimate of the compressor’s CFM rating.
Q: Why is CFM important for pneumatic tools?
A: CFM is crucial because it ensures that your air tools receive the consistent air flow they need to operate efficiently and effectively. Each pneumatic tool has a specific CFM requirement, which indicates the minimum volume of air needed for proper operation.
If the air compressor cannot meet this CFM requirement, the tool may experience reduced performance, stalling, or even damage. For example, an impact wrench may require 5 CFM to operate at full power.
If the air compressor supplies only 3 CFM, the impact wrench will not receive enough air to maintain its torque and speed, resulting in suboptimal performance. When selecting an air compressor, it’s essential to consider the CFM requirements of all the pneumatic tools you plan to use.
The compressor should have a CFM rating that meets or exceeds the highest CFM requirement among your tools. If you intend to operate multiple tools simultaneously, you’ll need to add their individual CFM requirements to determine the total CFM needed.
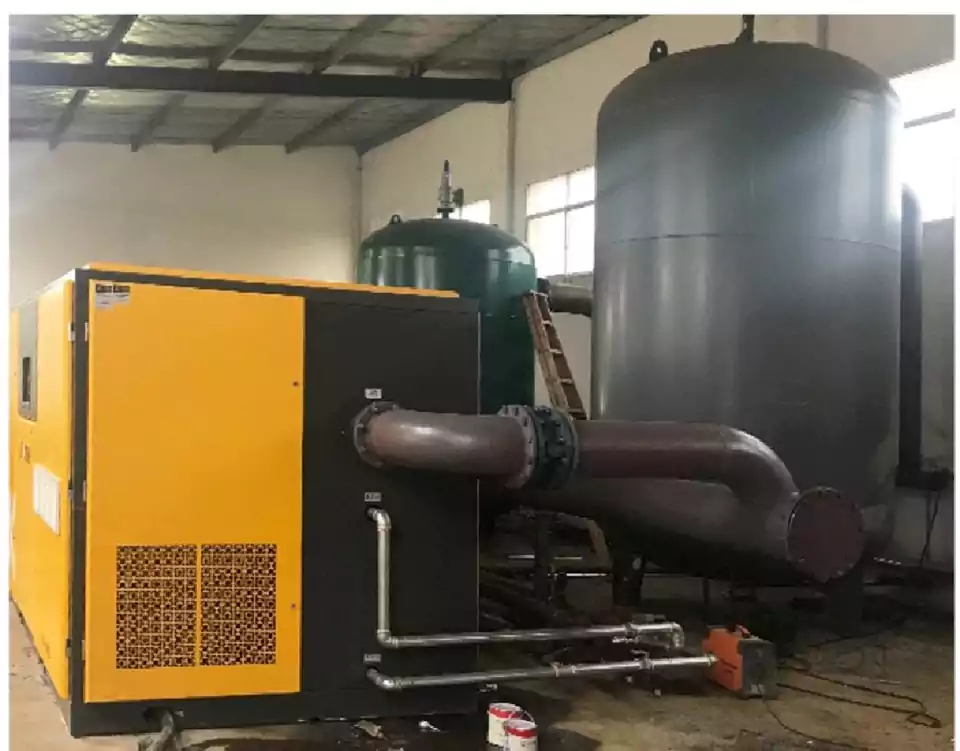
Matching the air compressor’s CFM output to your pneumatic tools’ requirements ensures that the tools receive a consistent and adequate supply of compressed air. This promotes optimal tool performance, increases productivity, and prolongs the life of your pneumatic equipment.
Q: Can I use a single air compressor for multiple tools with different CFM requirements?
A: Yes, but you need to ensure the compressor’s CFM output meets or exceeds the combined CFM requirements of the tools in use. When using multiple pneumatic tools simultaneously, it’s essential to add their individual CFM requirements to determine the total CFM needed.
For example, if you have three tools with CFM requirements of 5, 8, and 12 respectively, and you plan to use them at the same time, your air compressor should have a minimum CFM rating of 25 (5 + 8 + 12).
It’s also a good practice to add a safety margin of around 30% to account for any leaks or inefficiencies in the compressed air system. In the example above, the recommended compressor CFM rating would be: Required CFM = (5 + 8 + 12) × 1.3 = 32.5 CFM
When selecting an air compressor for multiple tools, consider the following factors:
- Maximum CFM requirement: Choose a compressor that can meet the highest CFM demand among your tools.
- Simultaneous tool use: Add the individual CFM requirements of tools that will be used at the same time to determine the total CFM needed.
- Future expansion: Consider any potential future needs for additional or higher-CFM tools, and select a compressor that can accommodate growth.
- Air storage: Incorporating air storage tanks can help buffer the compressed air supply, particularly when using multiple tools intermittently.
By ensuring that your air compressor’s CFM output meets the combined requirements of your pneumatic tools, you can maintain optimal performance and efficiency while avoiding potential issues such as tool stalling or damage.
For insights on managing CFM for multiple tools, visit TMI Compressed Air.
In conclusion, understanding CFM in air compressors is vital for selecting the right equipment and ensuring efficient operation. By considering the CFM requirements of your air tools and learning how to calculate and optimize CFM, you can significantly enhance your compressor’s performance and longevity.