The Rise of Rotary Screw Air Compressors
Rotary screw air compressors have become a staple in industrial applications due to their efficiency, durability, and versatility. These compressors use a rotary-type positive displacement mechanism, providing a steady and continuous supply of air.
The evolution of screw compressor technology has led to advanced designs and features that cater to a wide range of industrial needs. The rise of rotary screw compressors can be attributed to their numerous advantages over traditional piston compressors.
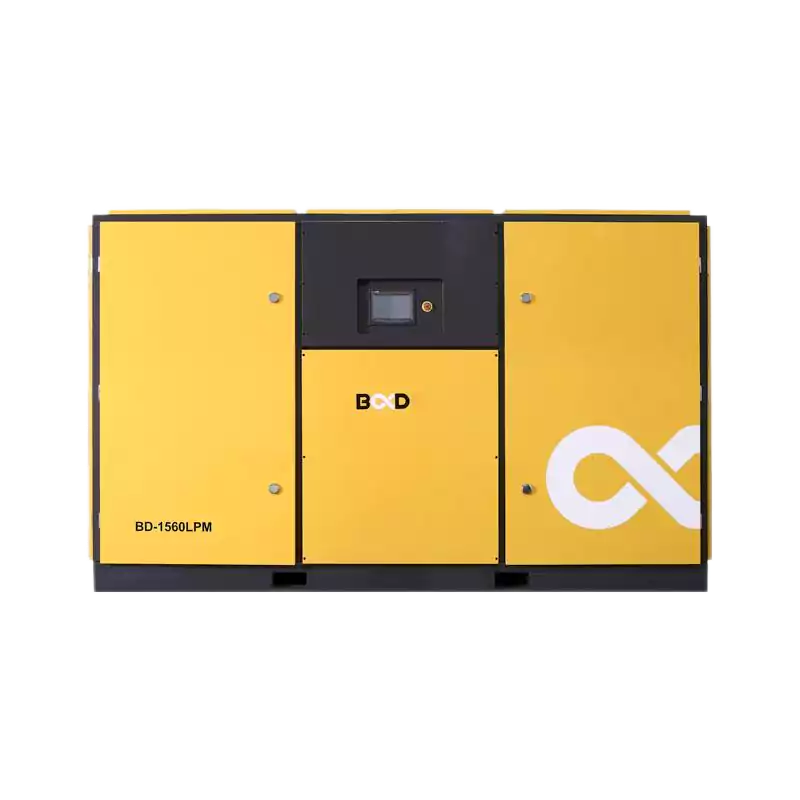
Screw compressors offer a more consistent and pulsation-free air supply, making them ideal for applications that require a steady flow of compressed air. They also operate at lower noise levels and have a smaller footprint compared to piston compressors, allowing for easier integration into various industrial settings.
Moreover, the energy efficiency of rotary screw compressors has significantly improved over the years. Advanced control systems, such as variable speed drives, enable compressors to adjust their output based on the demand, reducing energy consumption and operational costs.
The ability to recover heat generated during the compression process further enhances their energy efficiency, making them an eco-friendly choice for industries looking to reduce their carbon footprint.
Historical Development
The journey of rotary screw compressors began in the late 1930s, marking a significant improvement over the traditional piston compressors. Their design allows for less wear and tear, resulting in a longer service life and reduced maintenance costs.
The invention of the twin-screw compressor is credited to Swedish engineer Alf Lysholm, who developed the concept while working on gas turbines in the 1930s. Lysholm’s design featured two intermeshing rotors that compressed air as it moved through the compressor. This groundbreaking technology laid the foundation for the modern rotary screw compressor.
In the following decades, manufacturers continued to refine and improve the design of rotary screw compressors. The introduction of oil-injection technology in the 1950s further enhanced their performance and reliability. By injecting oil into the compression chamber, manufacturers were able to achieve better sealing, cooling, and lubrication, resulting in higher efficiency and longer component life.
As the demand for compressed air grew across various industries, so did the adoption of rotary screw compressors. Their compact size, quiet operation, and ability to deliver a consistent air supply made them the preferred choice for many industrial applications. Today, rotary screw compressors are widely used in manufacturing, automotive, food and beverage, and many other industries worldwide.
Technological Advancements
Modern rotary screw compressors incorporate advanced technologies, offering improved performance and energy efficiency. These advancements include variable speed drives, oil-free designs, and sophisticated control systems, ensuring optimal operation and cost-effectiveness.
One of the most significant technological advancements in rotary screw compressors is the introduction of variable speed drive (VSD) technology. VSD compressors can adjust their motor speed to match the air demand, resulting in substantial energy savings. By operating at the optimal speed for the required air output, VSD compressors minimize energy waste and reduce overall operational costs.
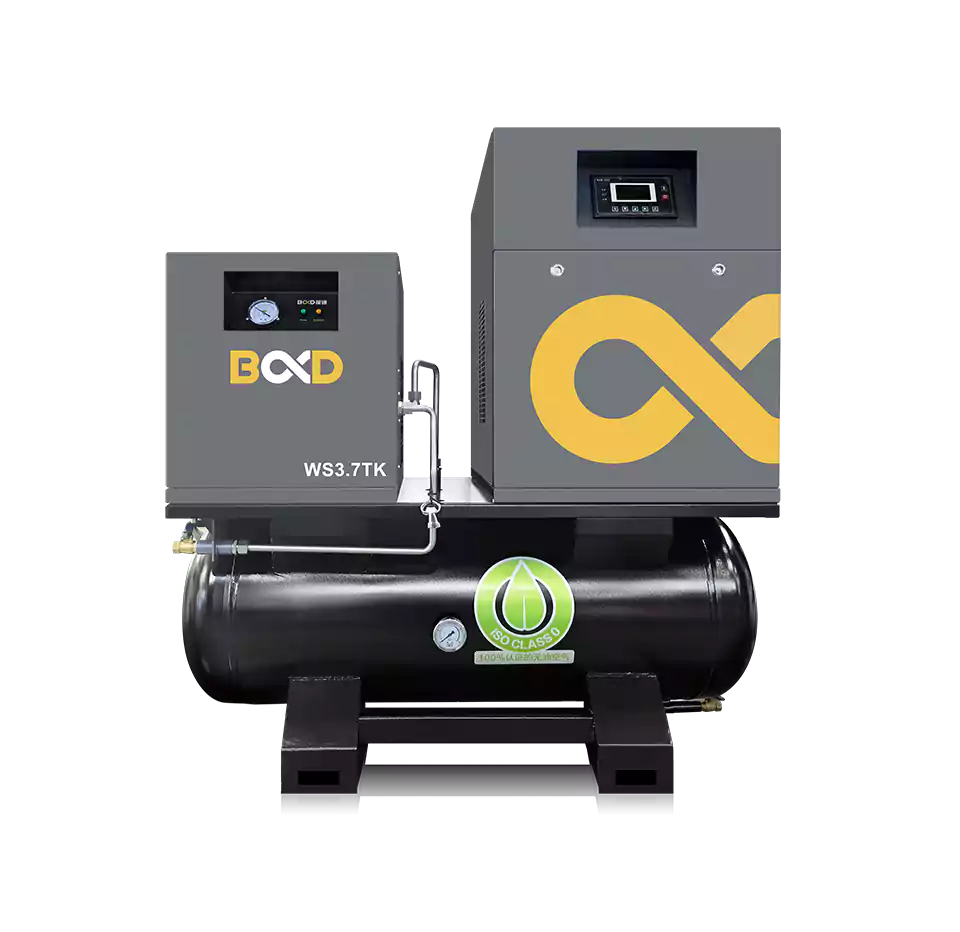
Another notable advancement is the development of oil-free rotary screw compressors. Traditional oil-injected compressors rely on oil for sealing, cooling, and lubrication, which can lead to oil contamination in the compressed air. Oil-free compressors, on the other hand, use specially designed coatings and seals to eliminate the need for oil in the compression chamber. This ensures a clean and oil-free air supply, crucial for industries such as food and beverage, pharmaceuticals, and electronics manufacturing.
Intelligent control systems have also revolutionized the way rotary screw compressors operate. These systems continuously monitor various parameters, such as air demand, pressure, and temperature, and adjust the compressor’s performance accordingly. Advanced control algorithms optimize energy consumption, maintain stable pressure levels, and predict maintenance requirements, ensuring the compressor operates at peak efficiency and reliability.
Furthermore, the integration of remote monitoring and IoT capabilities has made it easier for industries to manage and maintain their compressed air systems. Real-time data collection and analysis enable predictive maintenance, reducing downtime and extending the life of the equipment. Remote access to compressor performance data also allows for quick troubleshooting and optimization, even from remote locations.
As technology continues to advance, rotary screw compressors are expected to become even more efficient, reliable, and user-friendly. Manufacturers are constantly exploring new ways to enhance performance, reduce energy consumption, and minimize environmental impact, ensuring that rotary screw compressors remain the go-to choice for industrial compressed air needs.
Leading Manufacturers of Rotary Screw Air Compressors
Several companies have established themselves as leaders in the production of rotary screw air compressors, known for their innovative designs and reliable products.
Global Leaders
- Kaeser Kompressoren, a German company, has been at the forefront, offering compressors that are both powerful and energy-efficient. Kaeser has a strong presence in the global market, with a wide range of rotary screw compressors catering to various industrial applications. Their compressors are known for their durability, low maintenance requirements, and advanced control systems, making them a popular choice among industries worldwide.
- In the United States, companies like Ingersoll Rand and Sullair have a long history of producing high-quality screw compressors. Ingersoll Rand offers a comprehensive portfolio of rotary screw compressors, ranging from small workshop units to large industrial systems. Their compressors are designed for optimal performance, energy efficiency, and reliability, with features such as variable speed drives and heat recovery systems.
Sullair, another prominent US-based manufacturer, has been providing rotary screw compressors for over 50 years. Known for their rugged construction and reliable performance, Sullair compressors are widely used in demanding industrial environments, such as mining, construction, and oil and gas. The company’s focus on innovation has led to the development of advanced features, such as the Sullair Electronic Spiral Valve (ESV) technology, which optimizes compressor performance and efficiency.
Other notable global leaders in the rotary screw compressor market include Atlas Copco (Sweden), Gardner Denver (USA), Boge (Germany), and Hitachi (Japan). These companies have a strong presence in their respective regions and have contributed significantly to the advancement of rotary screw compressor technology.
Innovations in Compressor Technology
Manufacturers continuously innovate to meet the growing demands of various industries. Features like oil-free operation and improved energy efficiency are now common in new models, addressing environmental concerns and reducing operational costs.
One of the key areas of innovation in rotary screw compressor technology is the development of oil-free compressors. Traditional oil-injected compressors rely on oil for sealing, cooling, and lubrication, which can lead to oil contamination in the compressed air. This is a major concern for industries that require ultra-clean air, such as food and beverage, pharmaceuticals, and electronics manufacturing.
To address this issue, manufacturers have developed oil-free rotary screw compressors that use specially designed coatings and seals to eliminate the need for oil in the compression chamber. These compressors deliver 100% oil-free air, ensuring product quality and reducing the risk of contamination. Oil-free technology has also evolved to include water-injected compressors, which use water as a sealing and cooling medium, providing an environmentally friendly alternative to oil-based systems.
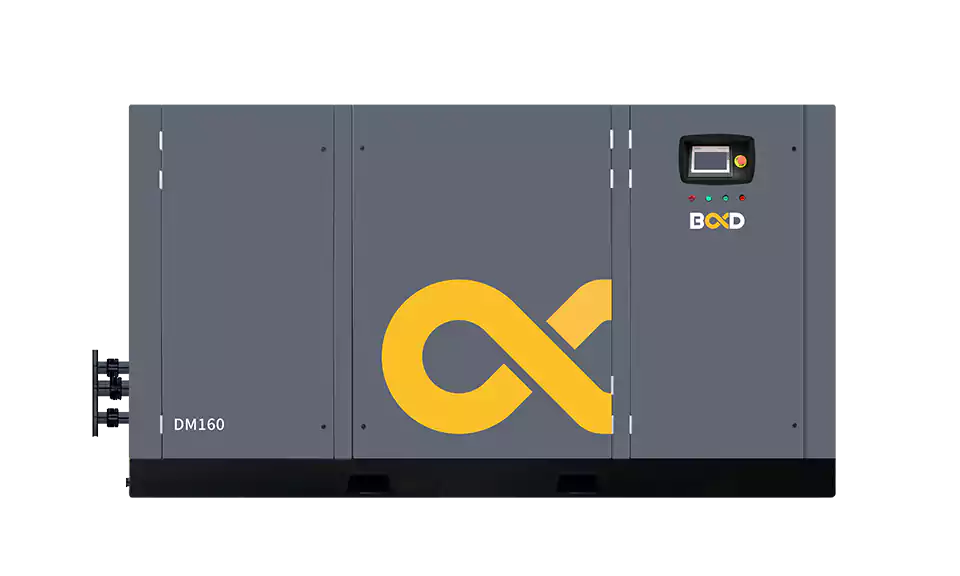
Another area of innovation is the integration of heat recovery systems in rotary screw compressors. During the compression process, a significant amount of heat is generated, which is typically dissipated through cooling systems. However, manufacturers have developed heat recovery systems that capture this waste heat and repurpose it for other applications, such as space heating, process heating, or water heating. By utilizing the waste heat, industries can reduce their overall energy consumption and improve their energy efficiency.
Manufacturers are also focusing on developing compressors with smaller footprints and modular designs. Compact compressors allow for easier installation in space-constrained environments, while modular designs enable customization and scalability based on specific industrial requirements. These innovations make rotary screw compressors more adaptable to various industrial settings and facilitate easier maintenance and servicing.
In addition to hardware innovations, manufacturers are investing in advanced control systems and software solutions. Intelligent control systems optimize compressor performance, monitor energy consumption, and predict maintenance requirements. Cloud-based platforms and IoT connectivity enable remote monitoring and control, allowing for real-time data analysis and proactive maintenance.
As industries continue to prioritize sustainability, energy efficiency, and operational excellence, manufacturers of rotary screw compressors are expected to drive further innovations. Collaborations with end-users, research institutions, and technology providers will play a crucial role in shaping the future of rotary screw compressor technology, ensuring that these compressors remain at the forefront of industrial compressed air solutions.
Applications of Rotary Screw Compressors
Rotary screw compressors are utilized in a myriad of applications, from manufacturing to construction, due to their reliability and efficiency.
Industrial Use
In sectors like manufacturing, automotive, and construction, rotary screw compressors provide a continuous air supply, essential for various tools and processes.
Manufacturing industries rely heavily on rotary screw compressors to power a wide range of pneumatic tools and equipment. These compressors provide a steady supply of compressed air for assembly lines, material handling systems, and automated machinery. In the automotive industry, rotary screw compressors are used for tasks such as powering air tools, paint spraying, and operating pneumatic presses.
Construction sites also benefit from the reliability and portability of rotary screw compressors. These compressors power tools like jackhammers, drills, and impact wrenches, enabling efficient and timely completion of construction projects. The rugged design and durability of rotary screw compressors make them well-suited for the demanding conditions found in construction environments.
In the oil and gas industry, rotary screw compressors play a crucial role in various processes, such as gas compression, well drilling, and pipeline transportation. These compressors are designed to handle the high pressures and flow rates required in oil and gas applications, ensuring reliable and efficient operations.
Specialized Applications
These compressors are also crucial in industries requiring high-quality air, such as pharmaceuticals, food and beverage, and electronics manufacturing, where they support critical processes and ensure product integrity.
In the pharmaceutical industry, rotary screw compressors provide clean, oil-free air for various applications, such as pill coating, tablet compression, and packaging. The strict regulations and quality standards in this industry necessitate the use of oil-free compressors to prevent contamination and ensure product safety.
Similarly, the food and beverage industry relies on rotary screw compressors for processes like bottling, canning, and packaging. Oil-free compressors are essential in this sector to maintain food safety and prevent contamination. Rotary screw compressors also provide the necessary air supply for pneumatic conveying systems, which transport ingredients and finished products within the production facility.
In the electronics manufacturing industry, rotary screw compressors supply clean, dry air for sensitive processes, such as PCB assembly, component placement, and clean room operations. The presence of moisture or contaminants in the compressed air can lead to product defects and failures, making oil-free rotary screw compressors the preferred choice for this industry.
Other specialized applications of rotary screw compressors include medical and dental equipment, where they power tools and instruments, and the textile industry, where they are used for air jet weaving and spinning processes. The versatility and reliability of rotary screw compressors make them suitable for a wide range of industries and applications, each with its unique requirements and challenges.
As industries continue to evolve and new applications emerge, rotary screw compressors are expected to adapt and innovate to meet the changing demands. Manufacturers are constantly working on improving the efficiency, reliability, and customization options of these compressors to cater to the diverse needs of various sectors. The ongoing advancements in rotary screw compressor technology will undoubtedly expand their use in both traditional and emerging industries, solidifying their position as a critical component in modern industrial processes.
Frequently Asked Questions
What makes rotary screw compressors preferable to piston compressors?
Rotary screw compressors offer greater efficiency, less noise, and a longer lifespan compared to piston compressors, making them ideal for continuous use in industrial environments.
Rotary screw compressors have several advantages over piston compressors that make them the preferred choice for many industrial applications:
- Efficiency: Rotary screw compressors are more energy-efficient than piston compressors. They operate at a constant speed and deliver a steady flow of compressed air, minimizing energy waste associated with the start-stop operation of piston compressors. The advanced control systems, such as variable speed drives, further optimize energy consumption by matching the compressor output to the air demand.
- Noise levels: Rotary screw compressors operate at significantly lower noise levels compared to piston compressors. The absence of reciprocating parts and the use of sound-attenuating enclosures contribute to their quiet operation. This is particularly important in industrial settings where noise pollution is a concern and in applications where the compressor is located close to the workspace.
- Lifespan and reliability: Rotary screw compressors have a longer lifespan and higher reliability compared to piston compressors. The rotary screw design involves fewer moving parts, which reduces wear and tear and extends the compressor’s service life. Additionally, the continuous operation of rotary screw compressors eliminates the stress associated with frequent starting and stopping, further enhancing their durability.
- Continuous operation: Rotary screw compressors are designed for continuous operation, making them suitable for applications that require a constant supply of compressed air. They can run 24/7 without the need for frequent rest periods, unlike piston compressors that require intermittent breaks to prevent overheating and ensure longevity.
- Air quality: Rotary screw compressors, especially oil-free models, deliver high-quality, clean air that is free from contaminants. This is crucial for industries that require pure, oil-free air, such as food and beverage, pharmaceuticals, and electronics manufacturing. Piston compressors, on the other hand, may introduce oil particles into the compressed air, necessitating additional filtration and treatment.
- Maintenance: While both types of compressors require regular maintenance, rotary screw compressors generally have lower maintenance requirements compared to piston compressors. The simple design and fewer moving parts of rotary screw compressors make them easier to service and maintain, reducing downtime and associated costs.
Although piston compressors still have their place in certain applications, such as small-scale or intermittent use, rotary screw compressors have become the preferred choice for most industrial compressed air needs. Their efficiency, reliability, and performance advantages make them a worthwhile investment for businesses looking to optimize their compressed air systems and minimize operational costs.
Can rotary screw compressors be used in sensitive industries?
Yes, rotary screw compressors are well-suited for industries that require high-quality, contaminant-free air, such as pharmaceuticals, food processing, and electronics manufacturing. Advancements in compressor technology, particularly the development of oil-free designs, have made rotary screw compressors a reliable choice for these sensitive applications.
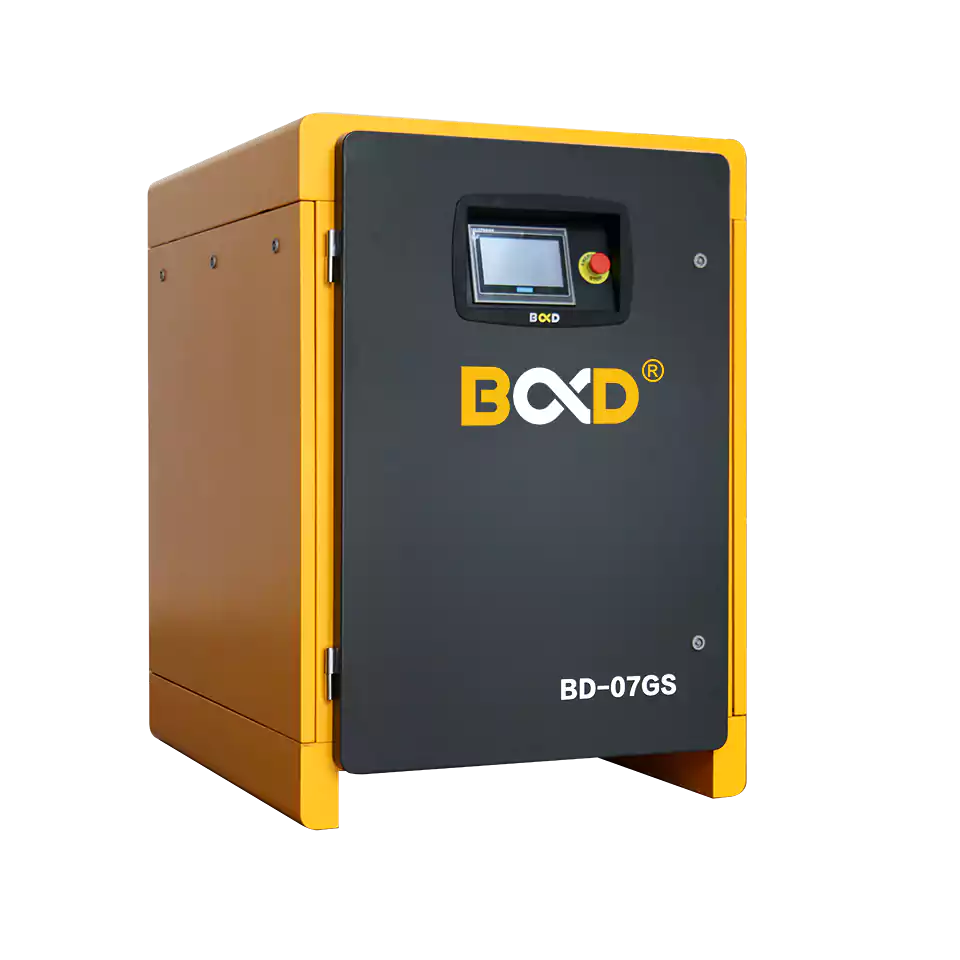
Oil-free rotary screw compressors use specially designed coatings and seals to eliminate the need for oil in the compression chamber. This ensures that the compressed air is 100% oil-free, preventing contamination and maintaining product integrity. Oil-free technology is crucial for industries with strict quality standards and regulations, as even trace amounts of oil can compromise product safety and quality.
In the pharmaceutical industry, oil-free rotary screw compressors provide clean air for various processes, such as tablet compression, pill coating, and packaging. The absence of oil contaminants ensures that the compressed air meets the stringent requirements for pharmaceutical manufacturing, reducing the risk of product recalls and ensuring patient safety.
Similarly, in the food and beverage industry, oil-free rotary screw compressors are essential for maintaining food safety and quality. These compressors supply clean air for processes like bottling, canning, and packaging, preventing contamination and preserving the taste and integrity of the products. The use of oil-free compressors also helps food and beverage manufacturers comply with strict hygiene standards and regulations.
In the electronics manufacturing industry, oil-free rotary screw compressors provide clean, dry air for sensitive processes, such as PCB assembly, component placement, and clean room operations. The presence of oil or moisture in the compressed air can lead to product defects, short circuits, and reduced reliability. Oil-free compressors ensure that the compressed air meets the stringent cleanliness requirements of electronics manufacturing, minimizing the risk of product failures and improving overall quality.
The use of oil-free rotary screw compressors in sensitive industries extends beyond the prevention of contamination. These compressors also offer other benefits, such as improved energy efficiency, reduced maintenance requirements, and lower operating costs. The absence of oil in the system eliminates the need for oil changes, oil filters, and oil disposal, simplifying maintenance and reducing environmental impact.
As industries continue to prioritize product quality, safety, and sustainability, the demand for oil-free rotary screw compressors is expected to grow. Manufacturers are continuously improving oil-free technology, developing new materials, coatings, and sealing solutions to enhance the performance and reliability of these compressors. The ongoing advancements in oil-free rotary screw compressor technology will further solidify their position as the preferred choice for sensitive industrial applications.
How do advancements in screw compressor technology benefit industries?
Innovations in screw compressor technology offer numerous benefits to industries, leading to higher efficiency, reduced energy consumption, and lower operating costs. These advancements help businesses optimize their compressed air systems, improve productivity, and enhance their bottom line.
One of the most significant advancements in screw compressor technology is the integration of variable speed drive (VSD) systems. VSD compressors can adjust their motor speed to match the air demand, resulting in substantial energy savings. By operating at the optimal speed for the required air output, VSD compressors minimize energy waste associated with the start-stop operation of fixed-speed compressors. This technology can lead to energy savings of up to 50%, significantly reducing electricity costs for industries.
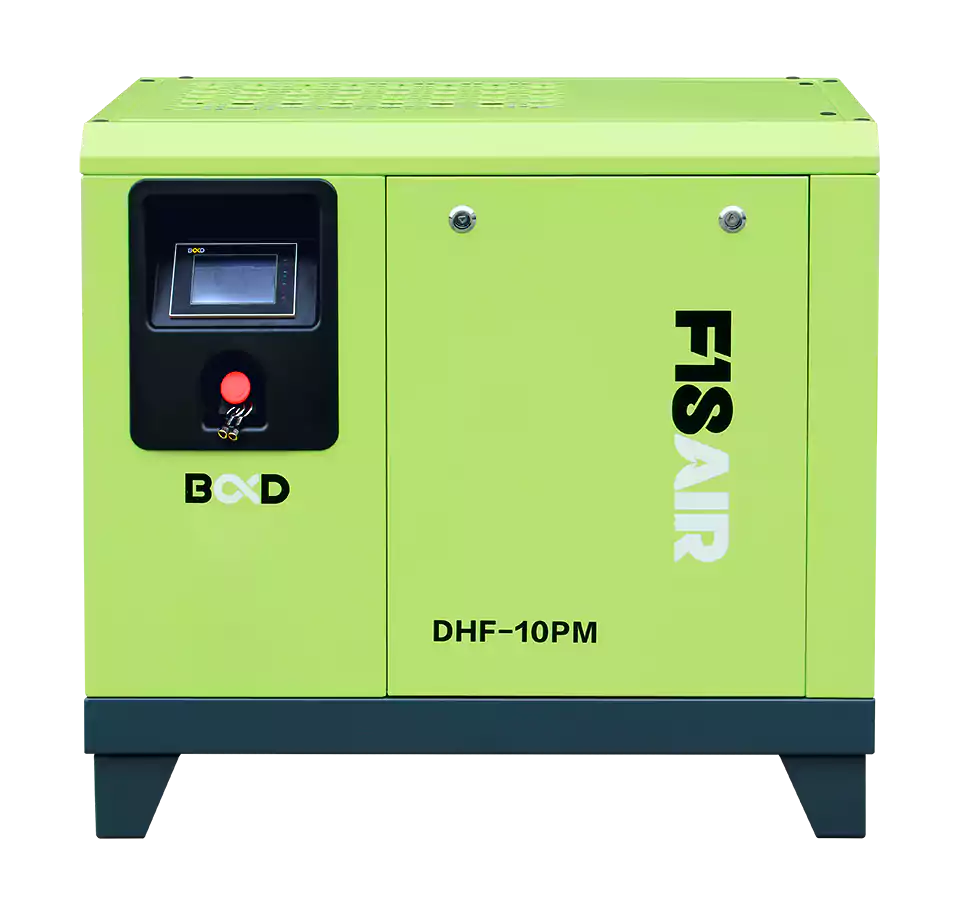
Another notable advancement is the development of heat recovery systems for rotary screw compressors. During the compression process, a significant amount of heat is generated, which is typically dissipated through cooling systems. However, heat recovery systems capture this waste heat and repurpose it for other applications, such as space heating, process heating, or water heating. By utilizing the waste heat, industries can reduce their overall energy consumption and improve their energy efficiency, leading to lower operating costs and a smaller carbon footprint.
Advancements in control systems and monitoring technologies also benefit industries by optimizing compressor performance and preventing downtime. Intelligent control systems continuously monitor various parameters, such as air demand, pressure, and temperature, and adjust the compressor’s performance accordingly. These systems can predict maintenance requirements, detect potential issues, and provide real-time data for proactive decision-making. Cloud-based platforms and IoT connectivity enable remote monitoring and control, allowing for seamless integration with existing industrial systems and facilitating predictive maintenance strategies.
Innovations in compressor design, such as the development of more compact and modular units, offer industries greater flexibility and ease of installation. Compact rotary screw compressors with smaller footprints allow for efficient use of space, making them suitable for industries with limited floor space or mobile applications. Modular designs enable customization and scalability, allowing businesses to adapt their compressed air systems to changing production requirements and future growth.
The advancements in oil-free rotary screw compressor technology, as discussed earlier, also provide significant benefits to industries. Oil-free compressors deliver clean, contaminant-free air, ensuring product quality and reducing the risk of contamination. This is particularly important for industries with strict quality standards, such as food and beverage, pharmaceuticals, and electronics manufacturing. The elimination of oil in the compression process also reduces maintenance requirements, as there is no need for oil changes, oil filters, or oil disposal, resulting in lower maintenance costs and increased uptime.
As industries strive for greater efficiency, sustainability, and competitiveness, the adoption of advanced rotary screw compressor technology becomes increasingly important. Manufacturers are continuously pushing the boundaries of innovation, developing new features and solutions to address the evolving needs of various industrial sectors. By embracing these technological advancements, industries can optimize their compressed air systems, reduce energy consumption, improve product quality, and enhance overall operational efficiency.
The benefits of advanced rotary screw compressor technology extend beyond individual businesses, contributing to the overall sustainability and competitiveness of industries on a global scale. As more companies adopt these innovative solutions, the collective impact on energy efficiency, carbon emissions, and resource conservation will be significant. The ongoing advancements in screw compressor technology will undoubtedly shape the future of industrial compressed air systems, driving industries towards a more sustainable and efficient future.
Conclusion
The evolution of rotary screw air compressors has revolutionized the industrial landscape, offering businesses a reliable, efficient, and versatile solution for their compressed air needs. From their humble beginnings in the 1930s to the cutting-edge technologies of today, rotary screw compressors have undergone a remarkable transformation.
The rise of rotary screw compressors can be attributed to their numerous advantages over traditional piston compressors, including higher efficiency, lower noise levels, and longer lifespans. These benefits have made them the preferred choice for a wide range of industrial applications, from manufacturing and construction to specialized sectors like pharmaceuticals and food processing.
Leading manufacturers have played a crucial role in driving the advancement of rotary screw compressor technology. Companies like Kaeser Kompressoren, Ingersoll Rand, and Sullair have consistently pushed the boundaries of innovation, developing compressors with improved performance, energy efficiency, and reliability. Their commitment to research and development has resulted in groundbreaking features, such as variable speed drives, oil-free designs, and sophisticated control systems.
The impact of rotary screw compressors extends far beyond their immediate applications. By providing industries with a dependable and efficient source of compressed air, these machines have enabled businesses to optimize their operations, reduce energy consumption, and lower operating costs. The adoption of advanced rotary screw compressor technology has also contributed to the overall sustainability and competitiveness of industries on a global scale.
As industries continue to prioritize efficiency, sustainability, and product quality, the demand for innovative rotary screw compressors is expected to grow. Manufacturers will undoubtedly continue to push the boundaries of technology, developing new solutions to address the evolving needs of various industrial sectors. The future of rotary screw compressors looks bright, with advancements in areas such as energy efficiency, oil-free technology, and IoT connectivity set to shape the industrial landscape for years to come.
In conclusion, the evolution and impact of rotary screw air compressors in industry cannot be overstated. These machines have transformed the way businesses operate, providing a reliable and efficient source of compressed air that has become indispensable in modern industrial processes. As technology continues to advance and new challenges arise, rotary screw compressors will undoubtedly remain at the forefront, driving industries towards a more sustainable, efficient, and competitive future.