Air compressors are pivotal in various industries, powering everything from pneumatic tools to HVAC systems. Their functionality, types, and applications are vast and varied. This article dives into the world of air compressors, breaking down their operation, types, and efficiency. Whether for industrial use or smaller projects, understanding air compressors can significantly impact productivity and outcomes.
Air compressors convert power, using an electric motor, diesel or gasoline engine, into potential energy stored in pressurized air. By one of several methods, an air compressor forces more and more air into a storage tank, increasing the pressure. When tank pressure reaches its engineered upper limit, the air compressor shuts off. The compressed air, then, is held in the tank until called into use.
The energy contained in the compressed air can be used for a variety of applications, utilizing the kinetic energy of the air as it is released. There are many methods of air compression, divided into either positive-displacement or negative-displacement types.
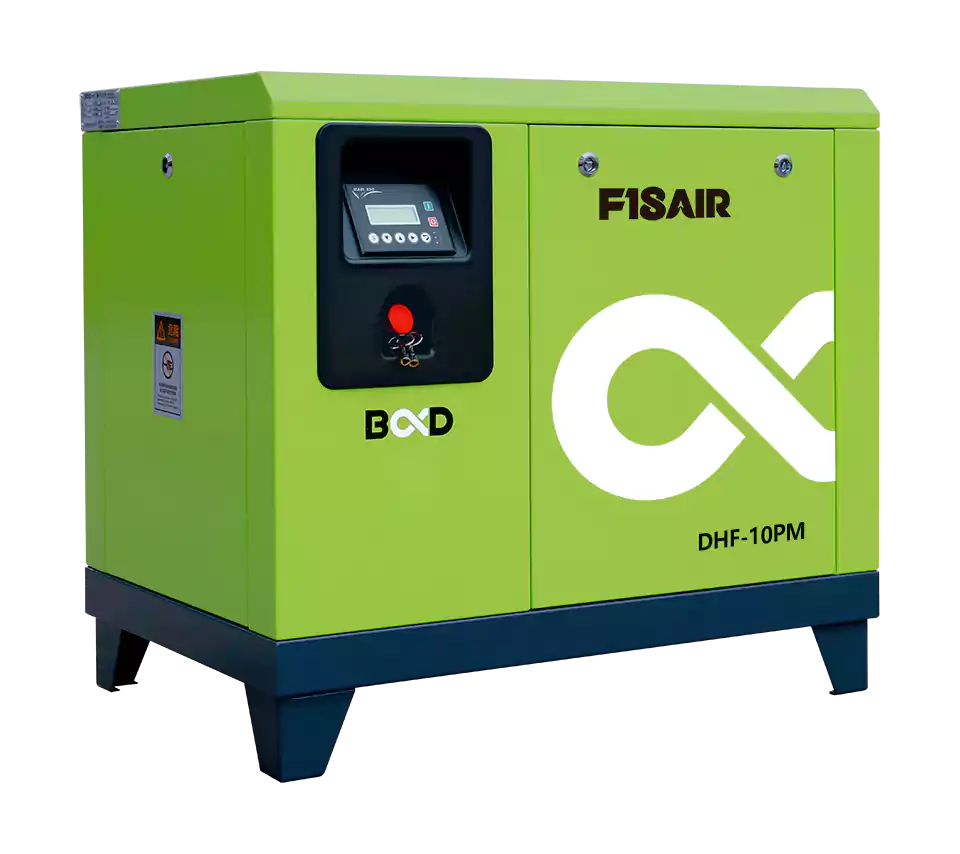
How Air Compressors Work
Air compressors function by drawing in atmospheric air, compressing it, and then releasing it into a storage tank. This process turns potential energy into kinetic energy, ready to be harnessed as needed. The basic components of an air compressor include a motor, an inlet and discharge valve, a pump, and a storage tank.
The compression process typically involves several stages:
- Intake: Air is drawn into the compressor pump through an inlet valve.
- Compression: The air is compressed, reducing its volume and increasing its pressure. This is done either by positive displacement (using pistons, screws, or vanes to reduce air volume) or dynamic displacement (using centrifugal force from an impeller).
- Discharge: The compressed air is released into the storage tank through a discharge valve. A check valve prevents the air from flowing back into the compressor.
- Storage: The compressed air is stored in the tank until needed. The tank pressure is regulated by a pressure switch, which turns the compressor motor on and off to maintain pressure within a set range.
- Delivery: When the compressed air is needed, it is released from the tank and delivered through an outlet valve to the application, such as a pneumatic tool or tire.
Understanding this process is key to selecting the right type and size of air compressor for your needs, as well as troubleshooting issues that may arise.
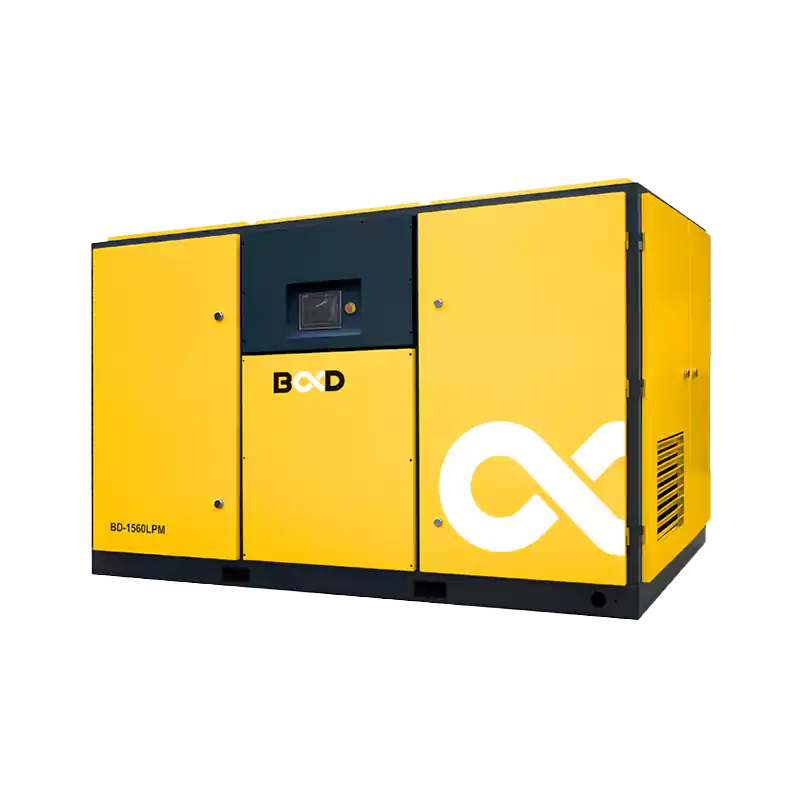
Positive vs. Dynamic Displacement
Two primary mechanisms define how air compressors work: positive and dynamic displacement.
Positive displacement compressors work by mechanically reducing the volume of air to increase its pressure. The most common types are:
- Reciprocating/piston compressors: Use pistons driven by a crankshaft to compress air
- Rotary screw compressors: Use two meshed helical screws to compress air
- Rotary vane compressors: Use a slotted rotor with sliding vanes to compress air
On the other hand, dynamic displacement compressors use an impeller’s rotational energy to compress the air, suitable for operations requiring rapid, high-volume air compression. The main types are:
- Centrifugal compressors: Use a rotating impeller to accelerate and then decelerate captured air
- Axial compressors: Use a series of airfoils to progressively compress air
The choice between positive and dynamic displacement depends on the application’s requirements for pressure, volume, and flow rate.
Types of Air Compressors
Several types of air compressors cater to various needs, from home DIY projects to large-scale industrial applications.
Rotary Screw Compressors
Rotary screw compressors are widely used in industrial settings. They contain two screws that interlock and rotate to compress air between them. This type is known for its efficiency and is available in both oil-injected and oil-free models.
Oil-injected rotary screw compressors use oil to lubricate, seal, and cool the compressed air. They are more energy-efficient and have a longer lifespan, but the compressed air may contain some oil, making them unsuitable for applications that require 100% oil-free air.
Oil-free rotary screw compressors, on the other hand, use special coatings and materials to operate without oil. They deliver pure, oil-free compressed air, crucial for industries such as food processing, pharmaceuticals, and electronics. However, they are generally more expensive and less energy-efficient than oil-injected models.
For a deeper understanding of rotary screw compressors, explore How Air Compressors Work: An Animated Guide by BigRentz.
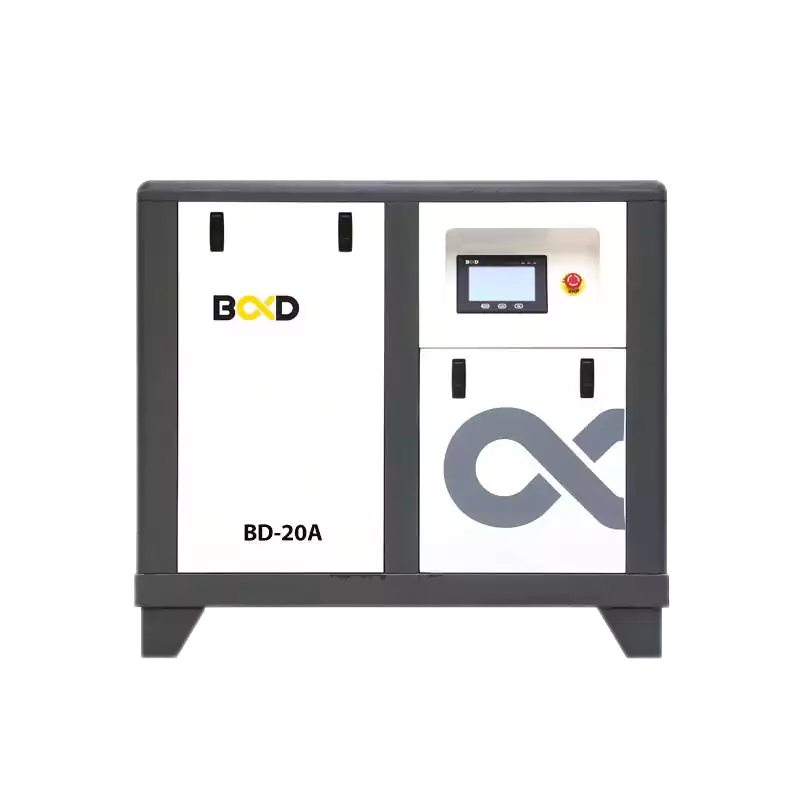
Reciprocating Compressors
Reciprocating compressors, or piston compressors, use pistons driven by a crankshaft to compress and displace air. They are commonly used for their ability to provide high pressure.
Single-stage reciprocating compressors have one cylinder and are suitable for lower pressure applications up to around 150 psi. Two-stage compressors have two cylinders and can achieve higher pressures up to around 200 psi. Multi-stage compressors with more than two cylinders can reach even higher pressures.
Reciprocating compressors are available in both lubricated and oil-free versions. Lubricated models use oil to reduce friction and wear, while oil-free models use special piston rings and cylinder linings.
For visual learners, this YouTube tutorial on compressor types offers a clear overview.
Centrifugal Compressors
Centrifugal compressors, or turbocompressors, leverage a rotating impeller’s high-speed to compress air. This type is ideal for applications needing continuous, high-volume air flow, such as in HVAC systems and large-scale industrial operations.
They operate by accelerating air through an inlet and into a rotating impeller. The impeller flings the air outwards at high velocity into a diffuser, which slows the air down, converting kinetic energy into pressure energy. The compressed air is then collected in a volute housing and discharged.
Centrifugal compressors are dynamic displacement machines, meaning they have a continuous flow of air rather than discrete volumes like positive displacement compressors. They are capable of very high flow rates but are limited in pressure, typically under 150 psi.
Enhancing Air Compressor Efficiency
Efficiency in air compressors is paramount to reducing operational costs and environmental impact. Factors such as the choice between electric motor air compressors and their gas-powered counterparts, the use of an air intake valve, and the specific compressor pump mechanism play significant roles in an air compressor’s efficiency.
Some key strategies for improving air compressor efficiency include:
- Proper sizing: Selecting an air compressor that matches the requirements of your application in terms of pressure and flow rate can prevent wasted energy from oversizing and inadequate performance from undersizing.
- Variable speed drives: These allow the compressor motor to adjust its speed based on air demand, reducing energy consumption during periods of low demand.
- Heat recovery: Compressing air generates a significant amount of heat, which can be captured and used for other processes, such as space heating or water heating.
- Leak prevention: Air leaks can waste a substantial amount of energy. Regular leak detection and repair can help maintain efficiency.
- Pressure reduction: Operating at the minimum required pressure for your application can save energy, as higher pressures require more power to achieve.
Oil-Injected vs. Oil-Free
The choice between oil-injected and oil-free compressors affects both the purity of the compressed air and the machine’s overall efficiency.
Oil-injected compressors are generally more durable and capable of higher pressures. The oil helps to lubricate, seal, and cool the compressor components, allowing for tighter clearances and reduced air leakage. However, the compressed air may contain some oil aerosols, which can be problematic for certain applications.
Oil-free compressors, while typically more expensive upfront, provide cleaner air that is essential in food, pharmaceutical, and electronics manufacturing. They may have slightly lower efficiency due to greater clearances and lack of oil cooling, but this can be offset by the elimination of oil filtration and disposal costs.
Ultimately, the choice depends on the specific needs of the application and the trade-offs between air purity, efficiency, and maintenance requirements.
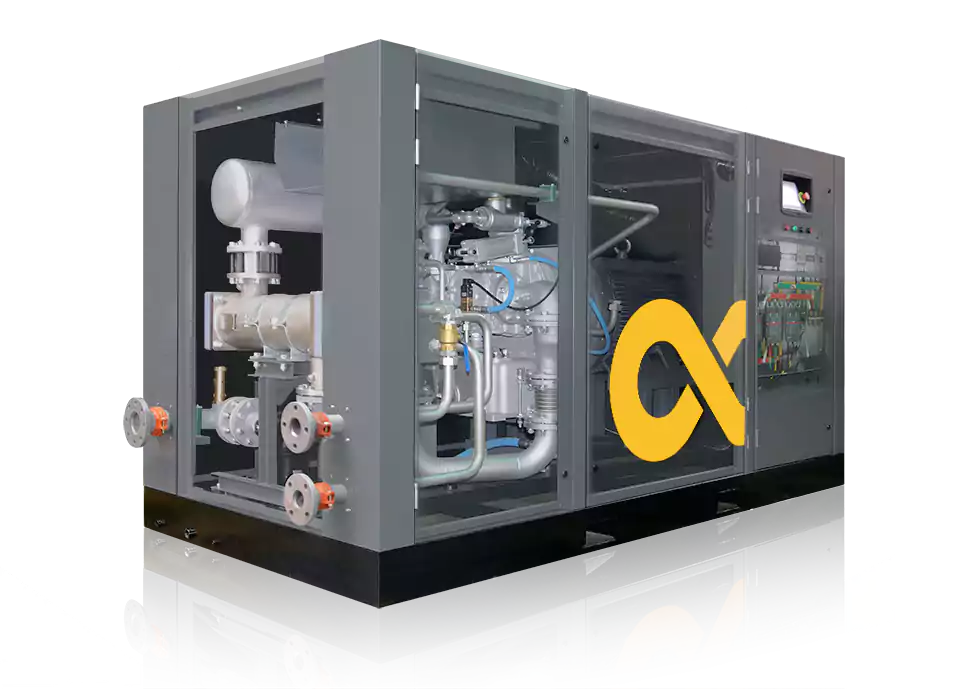
Frequently Asked Questions
Q: What is the difference between a rotary screw and a piston air compressor?
A: Rotary screw compressors use two interlocking screws to compress air, providing a continuous air flow, ideal for constant, high-demand applications. Piston (reciprocating) compressors use a piston and cylinder mechanism, better suited for high-pressure tasks with intermittent use.
Rotary screw compressors are generally more energy-efficient, quieter, and have a 100% duty cycle, meaning they can run continuously. Piston compressors are typically less expensive, easier to maintain, and better for smaller, intermittent use applications.
Q: How do I know if I need an oil-injected or oil-free air compressor?
A: Oil-injected compressors are typically used in industrial applications where air purity is less critical, and high performance is required. Oil-free compressors are essential in industries where air purity is paramount, such as in food and beverage, pharmaceuticals, and electronics manufacturing.
If your application is sensitive to oil contamination, such as painting, dental work, or food processing, an oil-free compressor is necessary. For general purpose use, such as powering tools or inflating tires, an oil-injected compressor is often sufficient and more cost-effective.
Q: Can air compressors be energy efficient?
A: Yes, selecting the right type of compressor for your needs, maintaining it properly, and optimizing its operation can significantly improve energy efficiency. Variable speed drives and energy-recovery systems can also enhance efficiency.
Other strategies include fixing air leaks, reducing system pressure, using proper sized piping, and implementing automatic shut-off controls. Regularly monitoring your compressed air system and making data-driven adjustments can help identify inefficiencies and opportunities for improvement.
By understanding the various types of air compressors, their working principles, and efficiency strategies, users can significantly improve their operational effectiveness. Whether for powering pneumatic tools, spray painting, or industrial manufacturing processes, air compressors are indispensable tools in modern industry.